A Primer on Molecular and Mechanical Recycling for Plastics
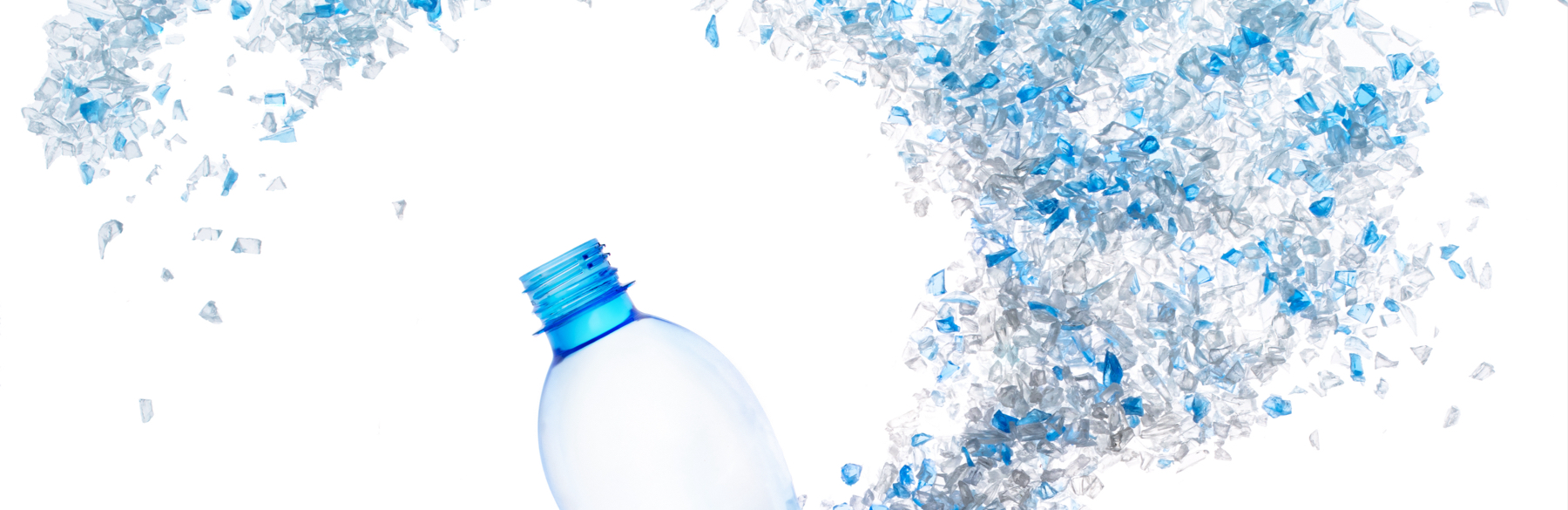
March 20,2024
Category: Sustainability
As the global economy steadily increases its focus on sustainability, the question of how to best deal with the more than 380 million tons of plastics produced globally each year is a challenging one for regulators, environmentalists, the waste management industry and packaging professionals. The modern era of mechanical recycling gained momentum in the 1970s and ‘80s, as these groups grappled with the steady increase in plastic production and its accumulation in landfills and as litter on land and in bodies of water.
According to the most recent data from the U.S. Environmental Protection Agency (EPA), only about 8.6 percent of the more than 35 million tons of plastic produced in the U.S. in 2018 was recycled. The rest wound up in landfills, burned for energy recovery or, even worse, as litter in the natural environment.
Mechanical recycling remains a vital part of the strategy for mitigating the buildup of plastic waste, and scaling up the waste management industry’s capacity for mechanical recycling is important. Truly meeting this challenge, however, calls for a significant advance in technology, which is where the emerging science of molecular recycling fits into the picture. Understanding the complexities of these two approaches to recycling is crucial for fostering a circular economy and achieving a more sustainable approach to plastic waste management.
Mechanical recycling, often also referred to as physical recycling, is the processing of plastics without altering their chemical structure. The mechanical recycling process involves a series of steps that alter the physical form of the material – think shredding, grinding or melting. These steps prepare the plastic material for additional processing that allows it to be used again in a new format.
The specific steps can vary depending on the polymer being recycled, but the process generally consists of:
Another challenge mechanical recycling methods is that not all plastic resins are good candidates for recycling. Some, such as polyvinyl chloride (PVC), cannot be recycled because of the high levels of hazardous additives used in their manufacturing. Others, such as polystyrene (PS), can be recycled, but generally aren’t because it is not profitable. Plastics in formats such as cling film and shopping bags are not recycled via curbside pickup because they can get caught in mechanical recycling equipment and jam rollers or other moving parts.
A third notable limitation for mechanically recycled plastics is the degradation and loss of polymer chain length plastics suffer as they’re shredded, ground or melted. This degradation weakens the material’s structural integrity and limits the number of times plastic can be recycled before stops being usable. To offset this loss of strength, virgin resins are often combined with PCR to help the material maintain its structural integrity.
Molecular recycling, also referred to as chemical or advanced recycling, involves breaking down plastic polymers into their molecular, monomer components through a depolymerization, dissolution or thermal cracking process. In depolymerization, the long polymer chains of plastic resins are broken down into their constituent monomers through chemical reactions or catalytic processes. The smaller molecular units can be used to create new polymers with quality equivalent to virgin plastics.
Dissolution is the process of breaking down polymers with a chemical agent such as a solvent. The polymer dissolves into the chemical solution, dispersing its monomers, which can then be further processed to recover the molecular components used to create new plastic materials.
Thermal cracking uses heat in an anaerobic (oxygen-free) environment to break down complex polymers into simpler compounds. These high temperatures cause chemical reactions that separate polymer chains into smaller hydrocarbon fragments. The outputs of this process are gases or liquids that can be further processed to create fuels, chemicals or other materials, such as new plastic resins.
While it comes with some of its own drawbacks, molecular recycling closes some of the gaps in the mechanical recycling system. While some types of plastic, such as PVC, PS, and formats such as plastic films, are not viable candidates for mechanical recycling, there are molecular recycling options for every type of plastic resin. Because molecular recycling methods break resins down into their composite monomers, they can be reformed into plastics with the same quality as virgin resins, avoiding the degradation and loss in quality that mechanically recycled materials experience. Molecular recycling methods do have their own drawbacks. As a nascent technology, infrastructure is very limited and expensive to build and operate. Most molecular recycling methods are also energy-intensive, which is an environmental issue of its own in an era when most energy is still produced by burning fossil fuels. Both of these limitations are likely to be less impactful as research continues and the technology improves, but they are important considerations in the present.
While both mechanical and molecular recycling methods have distinct advantages and drawbacks, dealing with the increasing amount of plastic produced each year requires a multiheaded approach to mitigating waste. Understanding both methods provides packaging teams with a clear understanding of the best ways to move forward. Where possible, substituting more recyclable materials in place of plastics, optimizing plastic packaging for curbside recycling and choosing materials made from PCR are the most direct ways packaging engineers can combat the global accumulation of plastic waste. Supporting initiatives that will boost mechanical recycling rates and research that will improve the efficiency of molecular recycling methods are also crucial to solving the problem.
If you need help evaluating options for reducing or eliminating plastic in packaging or sourcing materials made from PCR, get in touch. The sustainable packaging experts at Adept Group have helped brands in all industries improve packaging sustainability and implement changes the move the needle on reducing environmental harm, and they’re ready to get work helping your brand meet its sustainability goals.
According to the most recent data from the U.S. Environmental Protection Agency (EPA), only about 8.6 percent of the more than 35 million tons of plastic produced in the U.S. in 2018 was recycled. The rest wound up in landfills, burned for energy recovery or, even worse, as litter in the natural environment.
Mechanical recycling remains a vital part of the strategy for mitigating the buildup of plastic waste, and scaling up the waste management industry’s capacity for mechanical recycling is important. Truly meeting this challenge, however, calls for a significant advance in technology, which is where the emerging science of molecular recycling fits into the picture. Understanding the complexities of these two approaches to recycling is crucial for fostering a circular economy and achieving a more sustainable approach to plastic waste management.
The Basics of Mechanical Recycling
Mechanical recycling, often also referred to as physical recycling, is the processing of plastics without altering their chemical structure. The mechanical recycling process involves a series of steps that alter the physical form of the material – think shredding, grinding or melting. These steps prepare the plastic material for additional processing that allows it to be used again in a new format.The specific steps can vary depending on the polymer being recycled, but the process generally consists of:
- Collecting the plastic from various sources such as households (curbside recycling), businesses and recycling centers
- Sorting the plastics by polymer, e.g. polyethylene terephthalate (PET) high-density polyethylene (HDPE), polypropylene (PP), etc. and by color
- Cleaning the plastics to remove labels, adhesives and any other residues
- Shredding or grinding the plastics into smaller pieces or flakes • Melting the flakes to create a molten polymer
- Extruding the molten plastic to create pellets, sheets or other forms suitable for use in manufacturing
- In some instances, there may be further processing where pellets are cut into smaller pellets that make storage and transportation easier
- Using the recycled sheets or pellets in the manufacturing of new products or packaging
Another challenge mechanical recycling methods is that not all plastic resins are good candidates for recycling. Some, such as polyvinyl chloride (PVC), cannot be recycled because of the high levels of hazardous additives used in their manufacturing. Others, such as polystyrene (PS), can be recycled, but generally aren’t because it is not profitable. Plastics in formats such as cling film and shopping bags are not recycled via curbside pickup because they can get caught in mechanical recycling equipment and jam rollers or other moving parts.
A third notable limitation for mechanically recycled plastics is the degradation and loss of polymer chain length plastics suffer as they’re shredded, ground or melted. This degradation weakens the material’s structural integrity and limits the number of times plastic can be recycled before stops being usable. To offset this loss of strength, virgin resins are often combined with PCR to help the material maintain its structural integrity.
The Emerging Science of Molecular Recycling
Molecular recycling, also referred to as chemical or advanced recycling, involves breaking down plastic polymers into their molecular, monomer components through a depolymerization, dissolution or thermal cracking process. In depolymerization, the long polymer chains of plastic resins are broken down into their constituent monomers through chemical reactions or catalytic processes. The smaller molecular units can be used to create new polymers with quality equivalent to virgin plastics.Dissolution is the process of breaking down polymers with a chemical agent such as a solvent. The polymer dissolves into the chemical solution, dispersing its monomers, which can then be further processed to recover the molecular components used to create new plastic materials.
Thermal cracking uses heat in an anaerobic (oxygen-free) environment to break down complex polymers into simpler compounds. These high temperatures cause chemical reactions that separate polymer chains into smaller hydrocarbon fragments. The outputs of this process are gases or liquids that can be further processed to create fuels, chemicals or other materials, such as new plastic resins.
While it comes with some of its own drawbacks, molecular recycling closes some of the gaps in the mechanical recycling system. While some types of plastic, such as PVC, PS, and formats such as plastic films, are not viable candidates for mechanical recycling, there are molecular recycling options for every type of plastic resin. Because molecular recycling methods break resins down into their composite monomers, they can be reformed into plastics with the same quality as virgin resins, avoiding the degradation and loss in quality that mechanically recycled materials experience. Molecular recycling methods do have their own drawbacks. As a nascent technology, infrastructure is very limited and expensive to build and operate. Most molecular recycling methods are also energy-intensive, which is an environmental issue of its own in an era when most energy is still produced by burning fossil fuels. Both of these limitations are likely to be less impactful as research continues and the technology improves, but they are important considerations in the present.
While both mechanical and molecular recycling methods have distinct advantages and drawbacks, dealing with the increasing amount of plastic produced each year requires a multiheaded approach to mitigating waste. Understanding both methods provides packaging teams with a clear understanding of the best ways to move forward. Where possible, substituting more recyclable materials in place of plastics, optimizing plastic packaging for curbside recycling and choosing materials made from PCR are the most direct ways packaging engineers can combat the global accumulation of plastic waste. Supporting initiatives that will boost mechanical recycling rates and research that will improve the efficiency of molecular recycling methods are also crucial to solving the problem.
If you need help evaluating options for reducing or eliminating plastic in packaging or sourcing materials made from PCR, get in touch. The sustainable packaging experts at Adept Group have helped brands in all industries improve packaging sustainability and implement changes the move the needle on reducing environmental harm, and they’re ready to get work helping your brand meet its sustainability goals.