Busting Common Life Science Packaging Myths and Misconceptions
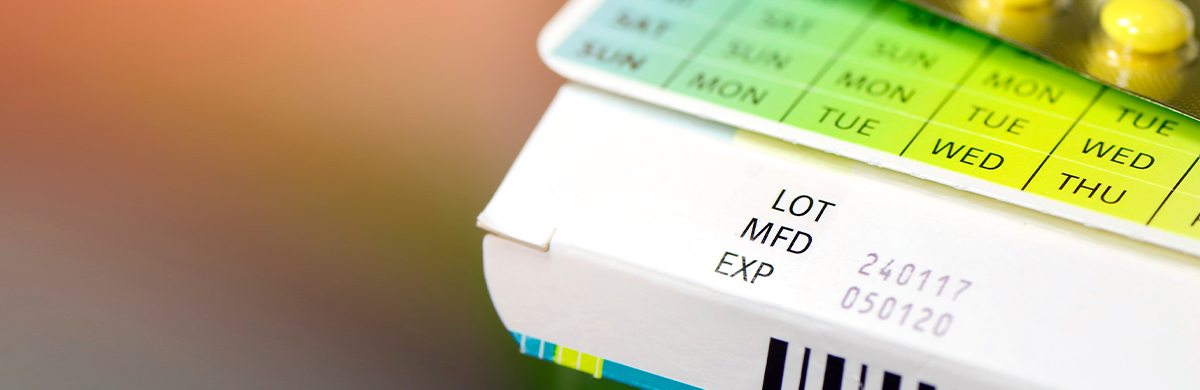.jpg)
May 10,2022
Category: Packaging Development
As packaging professionals continue to innovate and develop more sustainable, cost-effective, compliant and, most importantly, protective packaging solutions for products, many common myths and misconceptions persist. Distinguishing these myths from facts can help brands make more informed decisions on their packaging and clarify opportunities to reach packaging goals.
While a comprehensive breakdown of packaging myths could fill an entire book, this blog will examine common myths and misconceptions that relate to regulatory compliance, cold chain packaging and labeling.
Misconception #1 - Medical device packaging only needs to be tested once.
Medical device packaging, due to stringent requirements such as ISO 11607, ensures medical device packaging undergoes significant testing and qualification before reaching the consumer and will go through several tests during different periods of design and distribution. While the initial tests are extensive, packaging must be constantly validated throughout the product lifecycle. New devices must be tested for integrity, strength and microbial barrier protection, with each category having multiple tests used to evaluate the packaging. Compliance requires validation reports, along with installation, operational and performance qualification (IQ, OQ and PQ, respectively). Over time, regulations may change or a shift in packaging priorities may call for a redesign, so revalidation and qualification may be required periodically throughout a product’s lifecycle. All this means medical device packaging will not only be tested once, but multiple times during design to development and throughout distribution.
Misconception #2 - Regulations only apply to consumer-facing packaging and products.
While this may be accurate as it relates to product labeling - which has its own qualifications and requirements - the sterility and safety of the product is just as important for healthcare providers as it is for the patients and consumers. An experienced packaging engineer can ensure a package is qualified, compliant and prepared for distribution.
Misconception #3 - Compliance with one standard ensures compliance with all standards.
The standards with which a package must comply depends on too many factors for this to be accurate. Not only are there international and regional standards to follow, but depending on the manufacturer, the product, the retailers and the consumer, different regulations will apply. While compliance with one standard is a sign your packaging is on the right track, it does not guarantee the package will comply with all the relevant standards and regulations.
Misconception #1 - “Close enough” is good enough.
Cold chain packaging is one of the areas in which compliance is strictly regulated. If a biopharmaceutical product needs to remain between 1 and 5 degrees Celsius, but a shipping container varies between 0 and 7 degrees Celsius, the packaging has already failed. When a temperature-controlled product experiences an excursion outside its required range, it can become damaged and unusable, which becomes costly. In most cases, you’ll need to provide thorough and accurate documentation to prove the product’s temperature has been properly maintained, so “close enough” isn’t an option.
Misconception #2 - You only need to focus on the main touch points.
As a product moves from its origin to its destination, it can experience many touch points. Each of those touch points provides an opportunity for the product fall out of its required temperature range. The logistics for shipping need to account for each step of the products journey and ensure temperatures are controlled throughout. Most people who handle a product as it moves through its distribution environment aren’t temperature experts, so it’s essential to design a package that mitigates risks throughout distribution.
Misconception #3 - All cold chain solutions are the same.
Depending on the product and industry, cold chain strategies can vary significantly. Some solutions will regulate and monitor the temperature of each individual product in a shipper. Others maintain a uniform temperature for all the products in the container. A packaging engineer with thorough cold chain experience can recommend the solution that best suits product needs and cost requirements.
Misconception #4 - Medical device labeling is one-size-fits-all.
Labeling is an important part of packaging design, and labeling requirements cover not only the product, but also its packaging and instruction documents. ISO 13485 defines labeling as the “label, instructions for use, and any other information that is related to identification, technical description, intended purpose and proper use of the medical device.” This also includes risk management - hazardous materials and proper usage details are crucial to the safety of the consumer. Every individual product will have different uses and different instructions, so every label should be unique.
It can be easy to be led astray by these and other common misconceptions. If you need help sorting out how these concepts apply to your products and packaging, the Adept team has experience helping brands like yours solve their biggest challenges and create packaging that’s compliant, cost efficient and reliable. Get in contact with our team to learn more about how we can help you.
While a comprehensive breakdown of packaging myths could fill an entire book, this blog will examine common myths and misconceptions that relate to regulatory compliance, cold chain packaging and labeling.
Misconception #1 - Medical device packaging only needs to be tested once.
Medical device packaging, due to stringent requirements such as ISO 11607, ensures medical device packaging undergoes significant testing and qualification before reaching the consumer and will go through several tests during different periods of design and distribution. While the initial tests are extensive, packaging must be constantly validated throughout the product lifecycle. New devices must be tested for integrity, strength and microbial barrier protection, with each category having multiple tests used to evaluate the packaging. Compliance requires validation reports, along with installation, operational and performance qualification (IQ, OQ and PQ, respectively). Over time, regulations may change or a shift in packaging priorities may call for a redesign, so revalidation and qualification may be required periodically throughout a product’s lifecycle. All this means medical device packaging will not only be tested once, but multiple times during design to development and throughout distribution.
Misconception #2 - Regulations only apply to consumer-facing packaging and products.
While this may be accurate as it relates to product labeling - which has its own qualifications and requirements - the sterility and safety of the product is just as important for healthcare providers as it is for the patients and consumers. An experienced packaging engineer can ensure a package is qualified, compliant and prepared for distribution.
Misconception #3 - Compliance with one standard ensures compliance with all standards.
The standards with which a package must comply depends on too many factors for this to be accurate. Not only are there international and regional standards to follow, but depending on the manufacturer, the product, the retailers and the consumer, different regulations will apply. While compliance with one standard is a sign your packaging is on the right track, it does not guarantee the package will comply with all the relevant standards and regulations.
Cold Chain
Misconception #1 - “Close enough” is good enough.
Cold chain packaging is one of the areas in which compliance is strictly regulated. If a biopharmaceutical product needs to remain between 1 and 5 degrees Celsius, but a shipping container varies between 0 and 7 degrees Celsius, the packaging has already failed. When a temperature-controlled product experiences an excursion outside its required range, it can become damaged and unusable, which becomes costly. In most cases, you’ll need to provide thorough and accurate documentation to prove the product’s temperature has been properly maintained, so “close enough” isn’t an option.
Misconception #2 - You only need to focus on the main touch points.
As a product moves from its origin to its destination, it can experience many touch points. Each of those touch points provides an opportunity for the product fall out of its required temperature range. The logistics for shipping need to account for each step of the products journey and ensure temperatures are controlled throughout. Most people who handle a product as it moves through its distribution environment aren’t temperature experts, so it’s essential to design a package that mitigates risks throughout distribution.
Misconception #3 - All cold chain solutions are the same.
Depending on the product and industry, cold chain strategies can vary significantly. Some solutions will regulate and monitor the temperature of each individual product in a shipper. Others maintain a uniform temperature for all the products in the container. A packaging engineer with thorough cold chain experience can recommend the solution that best suits product needs and cost requirements.
Misconception #4 - Medical device labeling is one-size-fits-all.
Labeling is an important part of packaging design, and labeling requirements cover not only the product, but also its packaging and instruction documents. ISO 13485 defines labeling as the “label, instructions for use, and any other information that is related to identification, technical description, intended purpose and proper use of the medical device.” This also includes risk management - hazardous materials and proper usage details are crucial to the safety of the consumer. Every individual product will have different uses and different instructions, so every label should be unique.
Seeking Clarity
It can be easy to be led astray by these and other common misconceptions. If you need help sorting out how these concepts apply to your products and packaging, the Adept team has experience helping brands like yours solve their biggest challenges and create packaging that’s compliant, cost efficient and reliable. Get in contact with our team to learn more about how we can help you.