Considerations for Packaging Risk Assessment Part 2
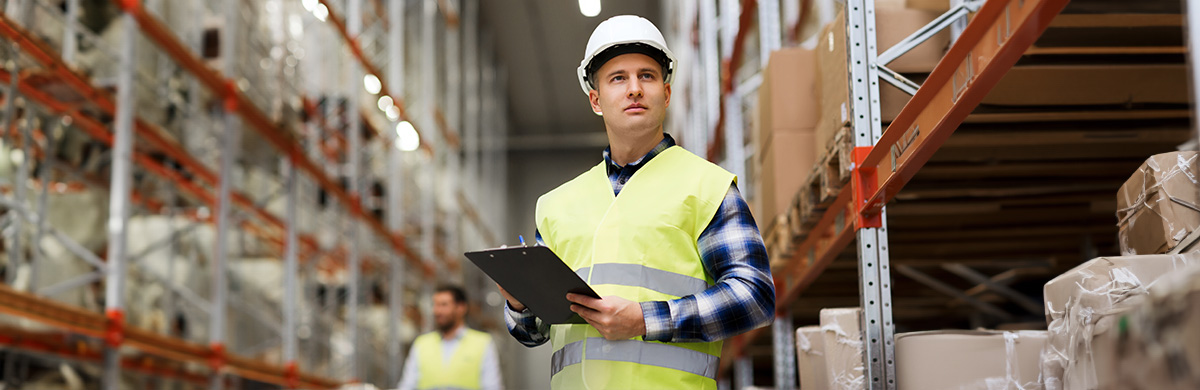
May 16,2024
Category: Cost Savings, E-Commerce, Packaging Development, Quality Optimization, Regulatory Compliance, Sustainability
Understanding the risks a product and its packaging face, from the packaging line through the package’s end of life, is essential for the packaging design and development process. Overlooking critical risks can drive excess costs, jeopardize a brand’s relationship with its consumers and even lead to fines and other regulatory consequences. To ensure all potential risks are accounted for, packaging teams must conduct a thorough packaging risk assessment at the outset of any packaging project.
A packaging risk assessment is a process used to evaluate potential risks associated with packaging materials and designs. This blog covers important factors related to environmental impact, supply chain challenges, quality assurance, and important documentation and communication considerations. To learn more about potential regulatory concerns, material hazards, product stability issues, transport and handling risks, and ergonomics and user safety considerations, check out our previous blog on this topic.
As global environmental concerns grow, consumers and regulators increasingly push for sustainable packaging solutions. Assessing environmental risks helps identify opportunities to reduce waste, minimize resource consumption, and lower the carbon footprint of packaging materials and distribution processes. Sustainable packaging solutions can lead to cost savings over time. For example, lighter and more compact packaging can reduce transportation costs and material expenses. Assessing environmental impact can help optimize packaging choices for efficiency and savings.
Excessive or non-recyclable packaging contributes to landfill waste. By assessing environmental impact risks, teams can design packaging that minimizes waste and promotes recycling or other responsible post-use scenarios, such as reuse or composting.
Companies that prioritize environmental sustainability often enjoy enhanced brand image. Environmentally conscious consumers, especially among younger generations, are more likely to support businesses that use eco-friendly packaging. A thorough assessment of environmental risks informs choices that lead to more sustainable outcomes, positioning the brand positively among these consumers.
Packaging teams must align their designs with the requirements of the product’s supply chain. Risk assessment should account for considerations such as labeling requirements, appropriate storage conditions and issues a product may face during distribution. It should also account for risks to packaging integrity, counterfeiting and potential tampering.
Assessing and addressing these and other supply chain risks ensures packaging remains resilient to disruptions caused by material shortages, natural disasters, political instability and unpredictable events such as global pandemics, ensuring business continuity. Failure to account for these risks can lead to supply chain interruptions such as delays and shortages in addition to increased costs.
Thorough assessment of these risks helps brands plan contingencies that mitigate against potential cost increases. Packaging teams that proactively plan for supply chain risks can help their brand gain a competitive advantage through preparedness for sudden challenges that helps ensure they meet consumer demand, potentially capitalizing on market opportunities caused my instability.
Assessing quality assurance risks ensures that packaging materials and designs maintain product integrity throughout the supply chain. Understanding these risks informs plans for regular testing and inspection procedures to ensure consistent packaging quality and performance. Thorough, well-planned testing and inspection processes help identify any deviations or issues that may pose risks during packaging and product handling.
Packaging defects or failures can pose safety risks to consumers. Sharp edges, loose components or contamination due to packaging materials can result in injuries or health hazards, and all can be avoided by identifying and planning for potential risks early in the packaging development process.
Quality assurance issues can impact compliance with the strict regulations governing the quality and safety of packaging materials and processes. As discussed in our previous blog on risk assessment, non-compliance can lead to legal consequences, product recalls and reputational damage. Knowing the quality assurance risks helps ensure adherence to these regulations.
Consistency in packaging quality is crucial to optimizing costs, meeting consumer expectations and protecting brand reputation. Assessing quality risks ensures that packaging processes and materials are consistent, reducing the likelihood of variations that can affect product presentation and safety.
Quality assessment is an ongoing process. By identifying and addressing quality assurance risks, companies can continuously improve their packaging materials, designs and manufacturing processes, helping to optimize costs and quality over time.
There are two ways to look at the importance of documentation when it comes to packaging risk assessment: risks associated with documentation and communication requirements and the importance of documenting risks and potential issues.
Documentation is often required to demonstrate compliance with industry regulations and standards. Without accurate records, it can be challenging to prove that packaging meets legal requirements. It also provides a clear and consistent record of packaging specifications, materials and quality standards. This ensures that everyone involved in the assessment process understands the requirements and expectations.
Proper documentation allows for the traceability of packaging materials and processes. In case of issues or defects, it becomes easier to identify the source of the problem and take corrective actions. Communication with suppliers is vital for sourcing quality packaging materials. Documented specifications and expectations help suppliers understand and meet the required standards, fostering better relationships.
Documenting packaging risks and potential issues helps teams identify and prioritize areas that need attention. It allows for systematic risk assessment and mitigation planning. Transparent documentation and communication foster trust among stakeholders, including suppliers, manufacturers and regulatory authorities, ensuring that everyone is on the same page regarding packaging requirements and risks.
Documentation and communication ensure that knowledge about packaging risks is not confined to individual employees. It allows for knowledge transfer within an organization, reducing dependence on specific individuals. In the event of a packaging-related crisis, well-documented information can be invaluable in managing the situation efficiently. Quick access to documentation helps in making informed decisions. It also serves as a valuable resource for training new employees or educating existing ones about packaging standards, risks and best practices.
If your brand is experiencing challenges related to these packaging risks or needs help evaluating potential risks for a new packaging product, Adept Group can help. Our nationwide team of packaging experts has experience helping brands overcome every type of packaging challenge efficiently, providing effective results and driving cost savings. Get in touch.
A packaging risk assessment is a process used to evaluate potential risks associated with packaging materials and designs. This blog covers important factors related to environmental impact, supply chain challenges, quality assurance, and important documentation and communication considerations. To learn more about potential regulatory concerns, material hazards, product stability issues, transport and handling risks, and ergonomics and user safety considerations, check out our previous blog on this topic.
Environmental Impact
As global environmental concerns grow, consumers and regulators increasingly push for sustainable packaging solutions. Assessing environmental risks helps identify opportunities to reduce waste, minimize resource consumption, and lower the carbon footprint of packaging materials and distribution processes. Sustainable packaging solutions can lead to cost savings over time. For example, lighter and more compact packaging can reduce transportation costs and material expenses. Assessing environmental impact can help optimize packaging choices for efficiency and savings.Excessive or non-recyclable packaging contributes to landfill waste. By assessing environmental impact risks, teams can design packaging that minimizes waste and promotes recycling or other responsible post-use scenarios, such as reuse or composting.
Companies that prioritize environmental sustainability often enjoy enhanced brand image. Environmentally conscious consumers, especially among younger generations, are more likely to support businesses that use eco-friendly packaging. A thorough assessment of environmental risks informs choices that lead to more sustainable outcomes, positioning the brand positively among these consumers.
Supply Chain
Packaging teams must align their designs with the requirements of the product’s supply chain. Risk assessment should account for considerations such as labeling requirements, appropriate storage conditions and issues a product may face during distribution. It should also account for risks to packaging integrity, counterfeiting and potential tampering.Assessing and addressing these and other supply chain risks ensures packaging remains resilient to disruptions caused by material shortages, natural disasters, political instability and unpredictable events such as global pandemics, ensuring business continuity. Failure to account for these risks can lead to supply chain interruptions such as delays and shortages in addition to increased costs.
Thorough assessment of these risks helps brands plan contingencies that mitigate against potential cost increases. Packaging teams that proactively plan for supply chain risks can help their brand gain a competitive advantage through preparedness for sudden challenges that helps ensure they meet consumer demand, potentially capitalizing on market opportunities caused my instability.
Quality Assurance
Assessing quality assurance risks ensures that packaging materials and designs maintain product integrity throughout the supply chain. Understanding these risks informs plans for regular testing and inspection procedures to ensure consistent packaging quality and performance. Thorough, well-planned testing and inspection processes help identify any deviations or issues that may pose risks during packaging and product handling.Packaging defects or failures can pose safety risks to consumers. Sharp edges, loose components or contamination due to packaging materials can result in injuries or health hazards, and all can be avoided by identifying and planning for potential risks early in the packaging development process.
Quality assurance issues can impact compliance with the strict regulations governing the quality and safety of packaging materials and processes. As discussed in our previous blog on risk assessment, non-compliance can lead to legal consequences, product recalls and reputational damage. Knowing the quality assurance risks helps ensure adherence to these regulations.
Consistency in packaging quality is crucial to optimizing costs, meeting consumer expectations and protecting brand reputation. Assessing quality risks ensures that packaging processes and materials are consistent, reducing the likelihood of variations that can affect product presentation and safety.
Quality assessment is an ongoing process. By identifying and addressing quality assurance risks, companies can continuously improve their packaging materials, designs and manufacturing processes, helping to optimize costs and quality over time.
Documentation and Communication
There are two ways to look at the importance of documentation when it comes to packaging risk assessment: risks associated with documentation and communication requirements and the importance of documenting risks and potential issues.Documentation is often required to demonstrate compliance with industry regulations and standards. Without accurate records, it can be challenging to prove that packaging meets legal requirements. It also provides a clear and consistent record of packaging specifications, materials and quality standards. This ensures that everyone involved in the assessment process understands the requirements and expectations.
Proper documentation allows for the traceability of packaging materials and processes. In case of issues or defects, it becomes easier to identify the source of the problem and take corrective actions. Communication with suppliers is vital for sourcing quality packaging materials. Documented specifications and expectations help suppliers understand and meet the required standards, fostering better relationships.
Documenting packaging risks and potential issues helps teams identify and prioritize areas that need attention. It allows for systematic risk assessment and mitigation planning. Transparent documentation and communication foster trust among stakeholders, including suppliers, manufacturers and regulatory authorities, ensuring that everyone is on the same page regarding packaging requirements and risks.
Documentation and communication ensure that knowledge about packaging risks is not confined to individual employees. It allows for knowledge transfer within an organization, reducing dependence on specific individuals. In the event of a packaging-related crisis, well-documented information can be invaluable in managing the situation efficiently. Quick access to documentation helps in making informed decisions. It also serves as a valuable resource for training new employees or educating existing ones about packaging standards, risks and best practices.
If your brand is experiencing challenges related to these packaging risks or needs help evaluating potential risks for a new packaging product, Adept Group can help. Our nationwide team of packaging experts has experience helping brands overcome every type of packaging challenge efficiently, providing effective results and driving cost savings. Get in touch.