Dassault Systèmes - Accelerate Sustainable Packaging in the Age of Experience
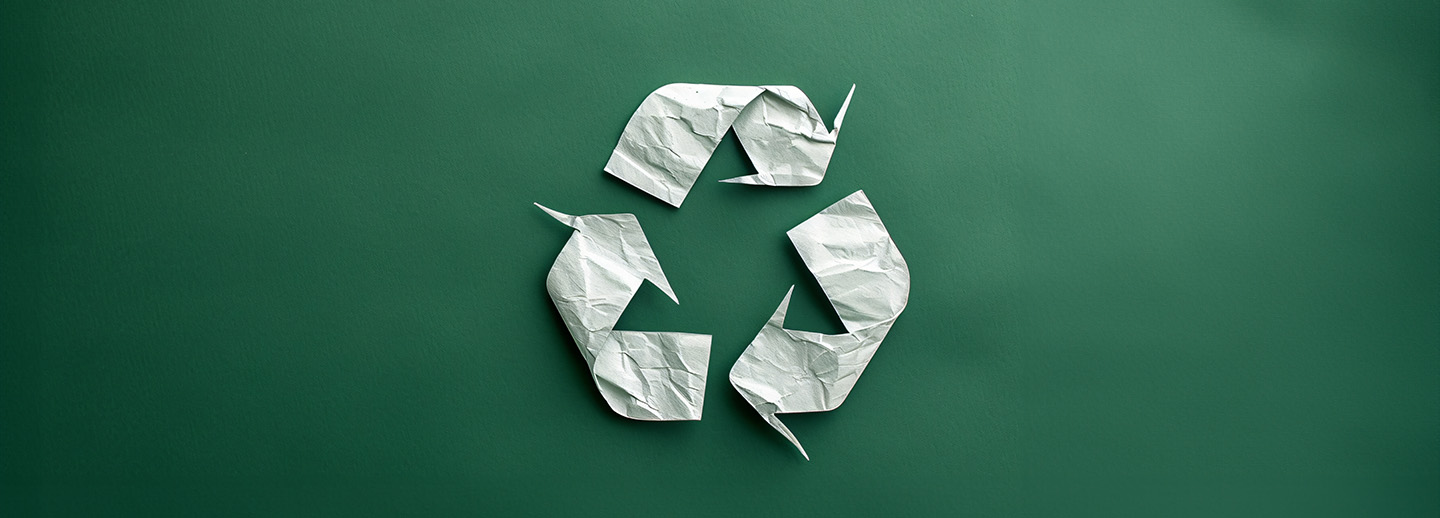
July 11,2024
Category: Sustainability
Episode Summary:
Sustainability remains at the forefront of the packaging design mindset with raw materials being assessed to help with aligning successful business practices and a circular process. However, the challenge remains to determine the durability of materials throughout a package’s life cycle. In episode four of our Unpacking Excellence podcast, we speak with Ray Wodar, Global Director of Business Consulting, Consumer Packaged Goods and Retail Industry, at Dassault Systèmes, about his team’s innovative virtual simulation software that allows you to view the performance of a package’s life cycle to save on any unnecessary costs down the line.
In this episode, we cover:
About Our Guest
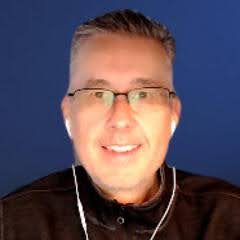
Ray Wodar
Global Director of Business Consulting, Consumer Packaged Goods and Retail Industry, Dassault Systèmes
For over 20 years, Ray Wodar has gained valuable experience in inventing, marketing and selling enterprise software solutions. He is an innovator in business, technology and marketing and holds a lead, global role at Dassault Systèmes in product strategy within the consumer packaged goods sector. He specializes in consumer products from pharmaceuticals to chemicals to food & beverage and more.
*At the time of recording, Dylan was a packaging design student at Michigan State University.
Listen to the Episode
00:00 - Intro
Powered by Adept Group, this is the Unpacking Excellence podcast, bringing together top packaging professionals to share insights and knowledge on all things packaging, Now, introducing Adept Group.
0:00:01 - Intro
Powered by Adept Group, this is the Unpacking Excellence podcast with Adept Group, bringing together top packaging professionals to share insight and knowledge on all things packaging. Now, introducing Adept Group.
0:00:16 - Adept Group
Well, thanks, Ray, for joining me today. I appreciate it and look forward to this conversation.
0:00:20 - Ray
Yeah, thanks.
0:00:21 - Adept Group
I think it's really interesting about you guys and the topic around accelerating sustainable packaging in the age of experience with Dassault Systèmes. Most packaging engineers are probably more familiar, and certainly with the SOLIDWORKS side, but Dassault Systèmes as a whole, and with all the different software that you guys have, it's really interesting what you guys are bringing to the table in terms of that whole packaging development process. So, we're really looking forward to this conversation.
0:00:43 - Ray
Yeah, for sure. I think most of our customers are familiar with the more mature areas of our capabilities around solid modeling and things like that, but, certainly, our platform now is enabling a more holistic capability of doing things like multi-physics simulation.
0:00:59 - Adept Group
Yeah, absolutely. So, yes, we dive into sustainability, and we always see a big push towards sustainability, and I feel, personally at least, sustainability has made that shift. It was a big buzzword for a while. I always joke that the only green that mattered was the dollar. But it's at a point where it's really not even its own thing. It's really just part of doing business. Companies have to be sustainable to be in business today. So, to me at least, it feels like we've made that shift to it actually being something that's being implemented. Now, the challenge is being put on package engineers. How do you actually reach these lofty goals that corporations are putting, these different alignments, goals and standards they're putting out there, into the public? And then, it gets pushed down to the package team to actually deliver on those sustainability goals.
0:01:40 - Ray
Right, absolutely. I think you're bang on with regards to the maturity level of most corporations now and on how they actually report and have corporate goals that are aligned now, certainly, with execution. Maybe in the past, it was more of a PR play to do greenwashing of their portfolios, but, certainly, I think the public at large, NGOs and governments are looking for media action to address this problem, so I think most businesses today are taking this seriously.
0:02:16 - Adept Group
Yeah, absolutely. Why don’t we just dive into what you guys are doing and how you’re supporting that process?
0:02:21 - Ray
Yeah, for sure. Our presentation focused on understanding the whole sustainable packaging ecosystem and how companies are approaching this difficult problem. It seems that everyone is looking for the magic bullet to solve this problem, and I think the key factor is that as we develop new technologies, it's just not any one thing. I think it's going to be a combination of multiple initiatives that will basically solve this problem. And we highlighted the fact that people are moving away from single-use to a more circular, specific business process where recycling is part of the process, but within the context of that circular economy, there's a lot of science and design as part of that process to make it massively more efficient with requirements from the design of the product itself and its performance, how it's manufactured, how packaging suppliers are using and utilizing those materials and then ultimately, how OEMs deploy that in any specific country or regulatory region.
So materials and the science of materials are going to be critical to solve this problem. Going forward, and just the aspects of doing things like bioplastics is a great example of trying to change the game. In the past, I think companies have tried to do some very basic capabilities and reduction of material waste, just from doing things like lightweighting and making their products leaner, if you will, and really cutting down on the amount of materials being used. But I think it's really a game-changer. Going forward, the new materials will be developed as part of this process.
0:04:14 - Adept Group
Yeah, no, I absolutely agree with that. I think one of the biggest challenges, like you said, is lightweighting. It was huge and still is huge. But you can only take that so far, and I think some of the brands are realizing too that they've almost taken it too far, and it's actually affecting them from a brand image point of view, and as much as they want to be sustainable, like a bottle, you only want it so thin until you start to think, wow, this is an inferior product.
So, I totally agree with that, and I think, on the raw material supply, certainly around that virtual model that your software, being able to really dive into the material, how it's going to perform, before that design process. Something we typically see is that pushback of trying new materials. They're not necessarily fully commercialized. How do you validate and prove out of new material? It can be challenging. So, certainly, I see where you guys can play a role in that.
0:04:58 - Ray
Yeah, for sure. And what we tried to focus on in the presentation was that it's just not one specific action that's required to make this process work. It's really this interconnected packaging value chain that has a domino effect on each part of the process.
So, as I said earlier, if you start with a new material from the very beginning, the entire design and optimization of that material have to be taken into consideration from the very start of the process and how it's manufactured, how it's then used, and from post-consumer, how it’s recycled and put back into the process of reusing that material again. So, the technologies that we provide, the aspect of understanding the cause and effect of all these downstream value chain impacts, I think are quite a value to things that haven't been proven or commercialized. If you can anticipate bottlenecks or changes to design or changes to your manufacturing process through these digital, virtual technologies, it's certainly reduced the cost and ramp-up time that's involved in implementing these new technologies. So, that's the message; you can't just take one siloed action without considering the bigger picture of how this downstream interaction happens with implementing these new techs.
0:06:20 - Adept Group
Yeah, perfect. So how does your software work? If you're looking at new material, as a packaging engineer, looking at 2020, goals have come down. We need to be more sustainable. We need to find new materials. What would they do? Can you walk me through that process and how it works from a packaging engineer's point of view?
0:06:41 - Ray
Yeah, for sure. If you’re starting from the very beginning of the process and getting into chemical engineering and a new molecule and how that’s being used in the development of the raw materials, that’s more of the upstream science.
But once the raw material is complete and commercialized, its performance characteristics can be modeled into these design and simulation systems so that a packaging engineer can basically use these digital, multi-physics engines to predict performance. So, basically, the packaging engineer gets the performance characteristics from the supplier, those raw materials, and that's defined within those multi-physics engines. You can then use your typical solid modeling tools to design out and mathematically precise dimensional information to build out the primary package and its interaction also with secondary and tertiary packaging. I think those are the exciting parts that people are looking at now as we've had quite simplistic models in the past where we've just had a primary package, whether it be a plastic bottle, glass, aluminum, whatever. Once you have those material properties, you can do some basic tests like squeeze tests, tip-over, top-load tests and drop tests. All those things can be done on those primary packages. And the exciting thing now is with more computing power that's readily available, and it's much cheaper, you can start to do more sophisticated co-simulation. Now, you can take that primary container, you can fill it with said product and put it in its secondary packaging. You can actually simulate what that product is going to experience during a shipping journey or how it's being used by the end customer and what their packaging experience is going to be when they're opening it and using the product in that second moment-of-truth scenario.
So, these are all models that can be built and proven out, and then, you get all that data back and try to predict the performance of the package and make sure that you're attaining all those goals as part of the targets that were originally put in a design brief or in a design target for the engineering of that product.
0:08:44 - Adept Group
That's great. So, I don't know how much you're able to share in general, but do you know any specific customer examples or processes in the packaging space that you can speak to?
0:08:53 - Ray
Yeah, for sure. I mean, a lot of our customers are using more advanced simulation, and since their task is to supply OEMs with more original packaging, obviously, they have to be aesthetically pleasing on the shelf. So, there are a lot of demands on making packages fresh and new and able to stand out on the shelf, and so, they're trying to not only please the OEM as far as making a unique package, but also achieving those sustainable goals. And it has to be cost-effective and comply with local regulations, maybe a post-consumer recycling requirement. It’s like a multi-dimensional problem that they have.
Our customers are putting these design constraints into these multi-physics engines, and it allows them to attain these design concepts much faster than they could have in the past. A lot of them are reducing things like time and cost by almost half, and they're also being able to deliver real concepts to their customers.
With the same amount of people, they can go through 10 different iterations and concepts where in the past, they'd only deliver one or two within the same time and context. So, it's really a productivity boost for our customers. That's allowing them to mitigate any risks and problems with the designs earlier in the process. It's fail fast, understand the constraints and requirements and then iterate and generate that new concept rapidly. And certainly, with other converging technologies like 3D printing, it allows you to really create these rapid concepts and prove them out very quickly, iterate through them, provide these concepts to their customers and have them experience those things very quickly and prove them out before they get into commercial scale-up.
0:10:45 - Adept Group
Yeah, I totally agree. We certainly hear that all the time, fail quickly, and I think, historically, without these sorts of technologies, you can get down the line pretty far before you realize that it’s just not a viable solution. So, be a bit upstream certainly.
0:10:59 - Ray
Yeah, you don't want to be in full-scale production and then find you have a problem and start to recall products or anything like that. That gets into a lot of cost and nasty business. There could be penalties involved or, God forbid, someone has a problem or gets hurt in the process of deploying or using a product.
0:11:17 - Adept Group
Absolutely. I think this is really good. I'm trying to think, from my end, is there anything else that you guys would want to add?
0:11:23 - Ray
Yeah, certainly. I think this is just the beginning of a journey for a lot of our customers. A lot of people get scared by the technology if they haven't invested a lot in simulation, or they see it as a big black box that they don't understand. That may have been in the past, maybe 10 years ago, you needed a staff of PhDs to develop these multi-physics models and deploy the technology. There was a lot of investment upfront before you really got any return. That's just not the case today.
Everything has gotten cheaper with computing power in the cloud. Now with high-performance computing, it's getting relatively cheap to do these very sophisticated co-simulations because you can just rent CPU time. Also, the simulation technology itself, all the methods that you'd have to develop from scratch before, a lot of that has been commercialized now. So, we're taking advantage of industry best practices. We're packaging those up and then deploying them in a commercial manner. So, people taking advantage of these technologies are really just getting the fruits and benefits of those people who were the industry leaders and who proved that simulation, and certainly in the CPG industry, is a worthwhile endeavor. And it's just not for automotive, aero and these high-tech industries; simulation can be used not only for design and aesthetics but also the simulation of packaging lines. So, a lot of the industrial engineering that goes on in delivering high-performance packaging and all these things, like costs, are coming down, and our customers are getting a good return on their investment in a much shorter timeframe than they have in past years.
0:13:06 - Adept Group
Yeah, I would just think about that. I remember my exposure to simulation. I left the company I was with at the time, but they've got much better I'm sure. But it was new to us. We bought the software and tested it, so, exactly, it was this big failed attempt, and it was taking about a couple of weeks to run the simulation.
0:13:34 - Ray
We have a lab right next door, and, in fact, simulation can be utilized hand in hand with physical testing, and that is the strategy that you can take now; that data that you do gather in physical labs can be run into machine learning algorithms to make that design iteration process that much faster. So, we're basically using AI and machine learning as a way to accelerate that productivity now. So, getting that data from physical labs, that's a massively important data resource. In the past, typically, it's maybe in a notebook somewhere and stored in someone’s head. But with new technology, and certainly in the realm of machine learning now, you can feed that data into machine learning algorithms, and that can make your simulation methods that much better going forward. It's a great data resource to have, for sure.
0:14:29 - Adept Group
Yeah, absolutely. So, you look towards the future, and as package engineers get more sophisticated in terms of this modeling and moving more towards this digital, fast, rapid turnaround with this, what do you see as the trends in this? Or, you're just starting out moving into this simulation, what do you think that looks like, or how do you suggest people get started?
0:14:48 - Ray Yeah, well, I think the trend in the future is going to be more of a value-chain-focused design and decision process because of the fact that packaging is really a multi-use product at the end of the day. And with the omnichannel that we have now, there's more and more direct-to-consumer packaging being developed, so the understanding of that whole transportation value chain of products has to be well understood in having one-off packaging for very specific usage requirements. I think this is going to be something that's going to be taken into consideration going forward. So, I think that's the future is this more holistic view of packaging and simulating it all the way out through the transportation value chain, and especially, too, when you're going to have robotics, drones and self-driving vehicles delivering these packages, I really don't think it's that far away, to be honest. I think we're getting very close to that becoming reality, and those considerations allow us to actually collect a lot of the data that's going to come from the telemetry, from those different vehicles and technologies, we'll be able to feed that back as a physical loop and understand the packaging journey a little bit better. And without these models, it's going to be hard to try to physically do that and try to predict the performance of packaging through that value chain.
So, to get started in this thing, you’ve got to dip your toe in the water and start to understand how this stuff works, and, certainly, just starting from the very beginning, primary packaging, using known materials and methods, I think that's the easiest way to get started. I think most design centers now are already fully trained up on mechanical modeling and automating a lot of that process. I think the next big push is really the simulation realm on how do you leverage all that digital data, that dimensional data and feed that into these machine learning algorithms, and that's just going to give the designer more freedom to be more creative and provide their customers a more rapid and innovative response rather than sweat all the details at the beginning of the process. Use those learning algorithms to come up with some really interesting and innovative designs, then focus more on the creative and provide that much better service to their OEM customers.
0:17:04 - Adept Group I think that’s a great point, especially if you're trying to push the boundaries and new materials. From a creative side, you may skew to being more conservative because it's so many different new elements. So, I think it's a really good point of having this type of system.
That would allow for some more creativity, allow for some more freedom in that design, being able to try unique concepts without the tooling costs and prototyping time. And now, I think there are some really great benefits beyond the scientific side of it and the technical side of it, but, certainly, around that creative design side as well.
0:17:37 - Ray
Yeah, I fully agree.
0:17:39 - Adept Group
Perfect. So, if somebody wants to find out some more information, what's the best way for them to do that?
0:17:40 - Ray
Well, we have our Dassault Systèmes website. 3ds.com would be a place to go and get all our industry-specific materials. We have 11 different industries that we focus on, and consumer packaged goods is certainly one of those verticals on our website. So, a lot of good materials there, a lot of good reference customer materials there, white papers on simulation, packaging design and then all our supporting materials from our brands like Atiya, SolidWorks and SIMULA are all on our website. That would be probably the best place to go, and outside of YouTube, too, if you want to see more interactive videos, we have a substantial library of presentations online on a lot of the social networks.
0:18:22 - Adept Group
Perfect. Well, Ray. I really appreciate it. Thank you for joining me today, and I look forward to speaking to you again in the future.
0:18:28 - Ray
Thanks very much for the opportunity.
0:18:30 - Outro
Thank you for listening to Unpacking Excellence with Adept Group. For more resources on all things packaging, head to our website, adeptpackaging.com. Don't forget to subscribe, and thanks again for listening.
About Adept Group
Adept Group is a premier packaging partner for some of the most iconic brands in the food & beverage, CPG, pharmaceutical, medical device and industrial industries. Our team has expertise in over 60 specialized areas of focus and is the go-to for packaging needs, from cost optimization to regulatory compliance to design and engineering services. We work with clients to help them maximize the value of their packaging with personalized strategies specific to their industry and goals. Throughout the years, we’ve helped clients save hundreds of millions of dollars through cost-saving approaches to packaging that also coincide with sustainability efforts, helping build trust and credibility with consumers. If you have a packaging challenge, we’re up for it. Get in touch with our team of packaging engineering experts today to get started.
Sustainability remains at the forefront of the packaging design mindset with raw materials being assessed to help with aligning successful business practices and a circular process. However, the challenge remains to determine the durability of materials throughout a package’s life cycle. In episode four of our Unpacking Excellence podcast, we speak with Ray Wodar, Global Director of Business Consulting, Consumer Packaged Goods and Retail Industry, at Dassault Systèmes, about his team’s innovative virtual simulation software that allows you to view the performance of a package’s life cycle to save on any unnecessary costs down the line.
In this episode, we cover:
- Accelerating sustainable packaging
- Opportunities for software simulation and new technologies
- Design and prototyping concepts for packaging engineers
About Our Guest
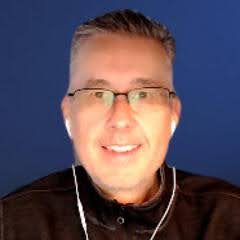
Ray Wodar
Global Director of Business Consulting, Consumer Packaged Goods and Retail Industry, Dassault Systèmes
For over 20 years, Ray Wodar has gained valuable experience in inventing, marketing and selling enterprise software solutions. He is an innovator in business, technology and marketing and holds a lead, global role at Dassault Systèmes in product strategy within the consumer packaged goods sector. He specializes in consumer products from pharmaceuticals to chemicals to food & beverage and more.
*At the time of recording, Dylan was a packaging design student at Michigan State University.
Listen to the Episode
00:00 - Intro
Powered by Adept Group, this is the Unpacking Excellence podcast, bringing together top packaging professionals to share insights and knowledge on all things packaging, Now, introducing Adept Group.
0:00:01 - Intro
Powered by Adept Group, this is the Unpacking Excellence podcast with Adept Group, bringing together top packaging professionals to share insight and knowledge on all things packaging. Now, introducing Adept Group.
0:00:16 - Adept Group
Well, thanks, Ray, for joining me today. I appreciate it and look forward to this conversation.
0:00:20 - Ray
Yeah, thanks.
0:00:21 - Adept Group
I think it's really interesting about you guys and the topic around accelerating sustainable packaging in the age of experience with Dassault Systèmes. Most packaging engineers are probably more familiar, and certainly with the SOLIDWORKS side, but Dassault Systèmes as a whole, and with all the different software that you guys have, it's really interesting what you guys are bringing to the table in terms of that whole packaging development process. So, we're really looking forward to this conversation.
0:00:43 - Ray
Yeah, for sure. I think most of our customers are familiar with the more mature areas of our capabilities around solid modeling and things like that, but, certainly, our platform now is enabling a more holistic capability of doing things like multi-physics simulation.
0:00:59 - Adept Group
Yeah, absolutely. So, yes, we dive into sustainability, and we always see a big push towards sustainability, and I feel, personally at least, sustainability has made that shift. It was a big buzzword for a while. I always joke that the only green that mattered was the dollar. But it's at a point where it's really not even its own thing. It's really just part of doing business. Companies have to be sustainable to be in business today. So, to me at least, it feels like we've made that shift to it actually being something that's being implemented. Now, the challenge is being put on package engineers. How do you actually reach these lofty goals that corporations are putting, these different alignments, goals and standards they're putting out there, into the public? And then, it gets pushed down to the package team to actually deliver on those sustainability goals.
0:01:40 - Ray
Right, absolutely. I think you're bang on with regards to the maturity level of most corporations now and on how they actually report and have corporate goals that are aligned now, certainly, with execution. Maybe in the past, it was more of a PR play to do greenwashing of their portfolios, but, certainly, I think the public at large, NGOs and governments are looking for media action to address this problem, so I think most businesses today are taking this seriously.
0:02:16 - Adept Group
Yeah, absolutely. Why don’t we just dive into what you guys are doing and how you’re supporting that process?
0:02:21 - Ray
Yeah, for sure. Our presentation focused on understanding the whole sustainable packaging ecosystem and how companies are approaching this difficult problem. It seems that everyone is looking for the magic bullet to solve this problem, and I think the key factor is that as we develop new technologies, it's just not any one thing. I think it's going to be a combination of multiple initiatives that will basically solve this problem. And we highlighted the fact that people are moving away from single-use to a more circular, specific business process where recycling is part of the process, but within the context of that circular economy, there's a lot of science and design as part of that process to make it massively more efficient with requirements from the design of the product itself and its performance, how it's manufactured, how packaging suppliers are using and utilizing those materials and then ultimately, how OEMs deploy that in any specific country or regulatory region.
So materials and the science of materials are going to be critical to solve this problem. Going forward, and just the aspects of doing things like bioplastics is a great example of trying to change the game. In the past, I think companies have tried to do some very basic capabilities and reduction of material waste, just from doing things like lightweighting and making their products leaner, if you will, and really cutting down on the amount of materials being used. But I think it's really a game-changer. Going forward, the new materials will be developed as part of this process.
0:04:14 - Adept Group
Yeah, no, I absolutely agree with that. I think one of the biggest challenges, like you said, is lightweighting. It was huge and still is huge. But you can only take that so far, and I think some of the brands are realizing too that they've almost taken it too far, and it's actually affecting them from a brand image point of view, and as much as they want to be sustainable, like a bottle, you only want it so thin until you start to think, wow, this is an inferior product.
So, I totally agree with that, and I think, on the raw material supply, certainly around that virtual model that your software, being able to really dive into the material, how it's going to perform, before that design process. Something we typically see is that pushback of trying new materials. They're not necessarily fully commercialized. How do you validate and prove out of new material? It can be challenging. So, certainly, I see where you guys can play a role in that.
0:04:58 - Ray
Yeah, for sure. And what we tried to focus on in the presentation was that it's just not one specific action that's required to make this process work. It's really this interconnected packaging value chain that has a domino effect on each part of the process.
So, as I said earlier, if you start with a new material from the very beginning, the entire design and optimization of that material have to be taken into consideration from the very start of the process and how it's manufactured, how it's then used, and from post-consumer, how it’s recycled and put back into the process of reusing that material again. So, the technologies that we provide, the aspect of understanding the cause and effect of all these downstream value chain impacts, I think are quite a value to things that haven't been proven or commercialized. If you can anticipate bottlenecks or changes to design or changes to your manufacturing process through these digital, virtual technologies, it's certainly reduced the cost and ramp-up time that's involved in implementing these new technologies. So, that's the message; you can't just take one siloed action without considering the bigger picture of how this downstream interaction happens with implementing these new techs.
0:06:20 - Adept Group
Yeah, perfect. So how does your software work? If you're looking at new material, as a packaging engineer, looking at 2020, goals have come down. We need to be more sustainable. We need to find new materials. What would they do? Can you walk me through that process and how it works from a packaging engineer's point of view?
0:06:41 - Ray
Yeah, for sure. If you’re starting from the very beginning of the process and getting into chemical engineering and a new molecule and how that’s being used in the development of the raw materials, that’s more of the upstream science.
But once the raw material is complete and commercialized, its performance characteristics can be modeled into these design and simulation systems so that a packaging engineer can basically use these digital, multi-physics engines to predict performance. So, basically, the packaging engineer gets the performance characteristics from the supplier, those raw materials, and that's defined within those multi-physics engines. You can then use your typical solid modeling tools to design out and mathematically precise dimensional information to build out the primary package and its interaction also with secondary and tertiary packaging. I think those are the exciting parts that people are looking at now as we've had quite simplistic models in the past where we've just had a primary package, whether it be a plastic bottle, glass, aluminum, whatever. Once you have those material properties, you can do some basic tests like squeeze tests, tip-over, top-load tests and drop tests. All those things can be done on those primary packages. And the exciting thing now is with more computing power that's readily available, and it's much cheaper, you can start to do more sophisticated co-simulation. Now, you can take that primary container, you can fill it with said product and put it in its secondary packaging. You can actually simulate what that product is going to experience during a shipping journey or how it's being used by the end customer and what their packaging experience is going to be when they're opening it and using the product in that second moment-of-truth scenario.
So, these are all models that can be built and proven out, and then, you get all that data back and try to predict the performance of the package and make sure that you're attaining all those goals as part of the targets that were originally put in a design brief or in a design target for the engineering of that product.
0:08:44 - Adept Group
That's great. So, I don't know how much you're able to share in general, but do you know any specific customer examples or processes in the packaging space that you can speak to?
0:08:53 - Ray
Yeah, for sure. I mean, a lot of our customers are using more advanced simulation, and since their task is to supply OEMs with more original packaging, obviously, they have to be aesthetically pleasing on the shelf. So, there are a lot of demands on making packages fresh and new and able to stand out on the shelf, and so, they're trying to not only please the OEM as far as making a unique package, but also achieving those sustainable goals. And it has to be cost-effective and comply with local regulations, maybe a post-consumer recycling requirement. It’s like a multi-dimensional problem that they have.
Our customers are putting these design constraints into these multi-physics engines, and it allows them to attain these design concepts much faster than they could have in the past. A lot of them are reducing things like time and cost by almost half, and they're also being able to deliver real concepts to their customers.
With the same amount of people, they can go through 10 different iterations and concepts where in the past, they'd only deliver one or two within the same time and context. So, it's really a productivity boost for our customers. That's allowing them to mitigate any risks and problems with the designs earlier in the process. It's fail fast, understand the constraints and requirements and then iterate and generate that new concept rapidly. And certainly, with other converging technologies like 3D printing, it allows you to really create these rapid concepts and prove them out very quickly, iterate through them, provide these concepts to their customers and have them experience those things very quickly and prove them out before they get into commercial scale-up.
0:10:45 - Adept Group
Yeah, I totally agree. We certainly hear that all the time, fail quickly, and I think, historically, without these sorts of technologies, you can get down the line pretty far before you realize that it’s just not a viable solution. So, be a bit upstream certainly.
0:10:59 - Ray
Yeah, you don't want to be in full-scale production and then find you have a problem and start to recall products or anything like that. That gets into a lot of cost and nasty business. There could be penalties involved or, God forbid, someone has a problem or gets hurt in the process of deploying or using a product.
0:11:17 - Adept Group
Absolutely. I think this is really good. I'm trying to think, from my end, is there anything else that you guys would want to add?
0:11:23 - Ray
Yeah, certainly. I think this is just the beginning of a journey for a lot of our customers. A lot of people get scared by the technology if they haven't invested a lot in simulation, or they see it as a big black box that they don't understand. That may have been in the past, maybe 10 years ago, you needed a staff of PhDs to develop these multi-physics models and deploy the technology. There was a lot of investment upfront before you really got any return. That's just not the case today.
Everything has gotten cheaper with computing power in the cloud. Now with high-performance computing, it's getting relatively cheap to do these very sophisticated co-simulations because you can just rent CPU time. Also, the simulation technology itself, all the methods that you'd have to develop from scratch before, a lot of that has been commercialized now. So, we're taking advantage of industry best practices. We're packaging those up and then deploying them in a commercial manner. So, people taking advantage of these technologies are really just getting the fruits and benefits of those people who were the industry leaders and who proved that simulation, and certainly in the CPG industry, is a worthwhile endeavor. And it's just not for automotive, aero and these high-tech industries; simulation can be used not only for design and aesthetics but also the simulation of packaging lines. So, a lot of the industrial engineering that goes on in delivering high-performance packaging and all these things, like costs, are coming down, and our customers are getting a good return on their investment in a much shorter timeframe than they have in past years.
0:13:06 - Adept Group
Yeah, I would just think about that. I remember my exposure to simulation. I left the company I was with at the time, but they've got much better I'm sure. But it was new to us. We bought the software and tested it, so, exactly, it was this big failed attempt, and it was taking about a couple of weeks to run the simulation.
0:13:34 - Ray
We have a lab right next door, and, in fact, simulation can be utilized hand in hand with physical testing, and that is the strategy that you can take now; that data that you do gather in physical labs can be run into machine learning algorithms to make that design iteration process that much faster. So, we're basically using AI and machine learning as a way to accelerate that productivity now. So, getting that data from physical labs, that's a massively important data resource. In the past, typically, it's maybe in a notebook somewhere and stored in someone’s head. But with new technology, and certainly in the realm of machine learning now, you can feed that data into machine learning algorithms, and that can make your simulation methods that much better going forward. It's a great data resource to have, for sure.
0:14:29 - Adept Group
Yeah, absolutely. So, you look towards the future, and as package engineers get more sophisticated in terms of this modeling and moving more towards this digital, fast, rapid turnaround with this, what do you see as the trends in this? Or, you're just starting out moving into this simulation, what do you think that looks like, or how do you suggest people get started?
0:14:48 - Ray Yeah, well, I think the trend in the future is going to be more of a value-chain-focused design and decision process because of the fact that packaging is really a multi-use product at the end of the day. And with the omnichannel that we have now, there's more and more direct-to-consumer packaging being developed, so the understanding of that whole transportation value chain of products has to be well understood in having one-off packaging for very specific usage requirements. I think this is going to be something that's going to be taken into consideration going forward. So, I think that's the future is this more holistic view of packaging and simulating it all the way out through the transportation value chain, and especially, too, when you're going to have robotics, drones and self-driving vehicles delivering these packages, I really don't think it's that far away, to be honest. I think we're getting very close to that becoming reality, and those considerations allow us to actually collect a lot of the data that's going to come from the telemetry, from those different vehicles and technologies, we'll be able to feed that back as a physical loop and understand the packaging journey a little bit better. And without these models, it's going to be hard to try to physically do that and try to predict the performance of packaging through that value chain.
So, to get started in this thing, you’ve got to dip your toe in the water and start to understand how this stuff works, and, certainly, just starting from the very beginning, primary packaging, using known materials and methods, I think that's the easiest way to get started. I think most design centers now are already fully trained up on mechanical modeling and automating a lot of that process. I think the next big push is really the simulation realm on how do you leverage all that digital data, that dimensional data and feed that into these machine learning algorithms, and that's just going to give the designer more freedom to be more creative and provide their customers a more rapid and innovative response rather than sweat all the details at the beginning of the process. Use those learning algorithms to come up with some really interesting and innovative designs, then focus more on the creative and provide that much better service to their OEM customers.
0:17:04 - Adept Group I think that’s a great point, especially if you're trying to push the boundaries and new materials. From a creative side, you may skew to being more conservative because it's so many different new elements. So, I think it's a really good point of having this type of system.
That would allow for some more creativity, allow for some more freedom in that design, being able to try unique concepts without the tooling costs and prototyping time. And now, I think there are some really great benefits beyond the scientific side of it and the technical side of it, but, certainly, around that creative design side as well.
0:17:37 - Ray
Yeah, I fully agree.
0:17:39 - Adept Group
Perfect. So, if somebody wants to find out some more information, what's the best way for them to do that?
0:17:40 - Ray
Well, we have our Dassault Systèmes website. 3ds.com would be a place to go and get all our industry-specific materials. We have 11 different industries that we focus on, and consumer packaged goods is certainly one of those verticals on our website. So, a lot of good materials there, a lot of good reference customer materials there, white papers on simulation, packaging design and then all our supporting materials from our brands like Atiya, SolidWorks and SIMULA are all on our website. That would be probably the best place to go, and outside of YouTube, too, if you want to see more interactive videos, we have a substantial library of presentations online on a lot of the social networks.
0:18:22 - Adept Group
Perfect. Well, Ray. I really appreciate it. Thank you for joining me today, and I look forward to speaking to you again in the future.
0:18:28 - Ray
Thanks very much for the opportunity.
0:18:30 - Outro
Thank you for listening to Unpacking Excellence with Adept Group. For more resources on all things packaging, head to our website, adeptpackaging.com. Don't forget to subscribe, and thanks again for listening.
About Adept Group
Adept Group is a premier packaging partner for some of the most iconic brands in the food & beverage, CPG, pharmaceutical, medical device and industrial industries. Our team has expertise in over 60 specialized areas of focus and is the go-to for packaging needs, from cost optimization to regulatory compliance to design and engineering services. We work with clients to help them maximize the value of their packaging with personalized strategies specific to their industry and goals. Throughout the years, we’ve helped clients save hundreds of millions of dollars through cost-saving approaches to packaging that also coincide with sustainability efforts, helping build trust and credibility with consumers. If you have a packaging challenge, we’re up for it. Get in touch with our team of packaging engineering experts today to get started.