Maintaining and Monitoring Cold Chain Packaging
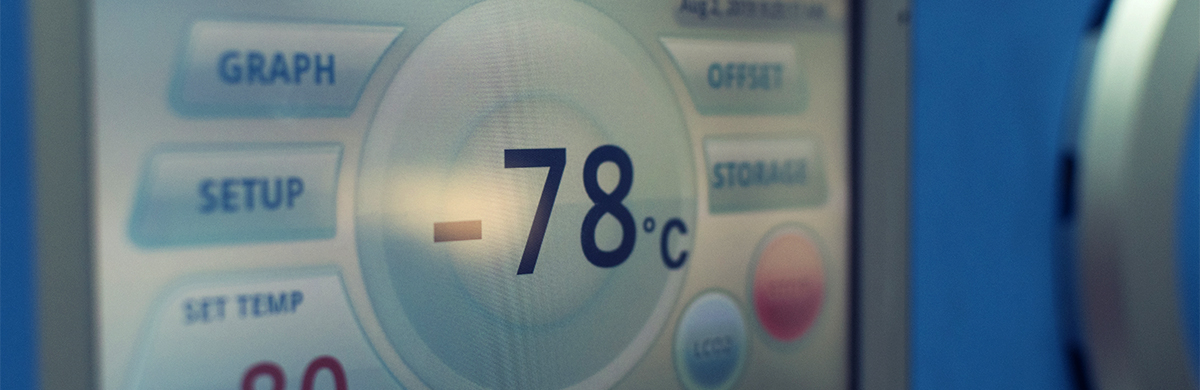.jpg)
In recent years, cold chain packaging has been more important than ever. The cold chain played a critical role in COVID-19 vaccine distribution, and increasing global demand for high-end food products is raising its profile in the food & beverage space. As cold chain technology develops and demand for controlled-temperature shipping increases, it’s important for brands to understand their cold chain packaging options and the role it plays in preserving products during shipping.
The cold chain requires package design and distribution methods that are specifically engineered to maintain a product’s temperature from production through final distribution. This helps prevent temperature excursions that can affect the quality or efficacy of products. Efficient cold chain shipping uses monitoring to track temperatures and minimizes the number of hand-offs between the shipping origin and destination. To successfully accomplish this, brands must utilize specific technology and distribution practices and adhere to regulatory requirements and standards set by organizations such as the U.S. Food and Drug Administration (FDA) and The International Council for Harmonisation of Technical Requirements for Pharmaceuticals for Human Use (ICH).
Every product that requires cold chain packaging will have different needs, including the design of temperature-controlled shippers and shipping processes and supply chain routes. Many pharmaceuticals must remain at a certain temperature to secure the active ingredients. Some food products, such as dairy and poultry, must be stored at 41 degrees Fahrenheit as outlined by the FDA’s Food Code. Guidance on regulatory requirements are outlined by organizations like the World Health Organization (WHO), China’s GSP, the EUMD, and The International Air Trasport Association (IATA). A successful cold chain strategy complies with these standards and regulations to ensure shippers function as intended.
When done properly, cold chain packaging design should maximize both protection against typical shipping hazards (impact, vibration, exposure to moisture, etc.) and protection against temperature excursions. Interactions between components, materials and processes can make developing a cold chain solution complex, as they can impact the performance of the package. For products that require temperature-controlled shipping, planning for cold chain logistics should begin during the early design and manufacturing stage of the product.
Active Cold Chain Solutions
Active systems consist of shippers or containers that feature temperature-controlled technology such as electric or battery-powered cooling. This includes built-in cooling units or dry ice usage. Active cold chain systems are most effective for larger shipments because the cooling system controls and maintains the temperature of the entire payload.Passive Cold Chain Solutions
Passive systems utilize design technologies that typically include polyurethane or polystyrene insulation or vacuum-insulated panels that help keep a product at a set temperature for 96 hours or more. Passive systems are typically better for maintaining products that need to stay within a specific temperature range, since active systems are more prone to internal freezing. While passive systems are generally more effective, they are often more complex and more expensive. Additionally, passive systems have time limits that may not work well in distribution environments that are prone to delays.For that reason, it’s important to have a comprehensive strategy for qualification of the system. This will inform relevant parties of the most appropriate and cost-effective approach to achieving their shipping goals. Prior to the qualification phase, potential risks should be identified, and related mitigation measures should be determined. Potential risks should be revisited as needed after subsequent testing phases to address solutions to identified risks. Risk assessment helps ensure that the proposed qualification procedure matches the intended use. In addition, User Requirement Specification (URS) lists the attributes, which are explicit and verifiable, assigned by the user prior to a qualification test to establish performance limits.
Keeping a product safe and from losing its effectiveness requires a comprehensive approach that starts during preparation and manufacturing of the product and continues through final delivery. A Process Flow Diagram (PFD) will help you identify potential solutions by mapping out the potential risks in the supply chain and solutions to monitor the shipment. Through this practice, packaging engineers can introduce designs and technology to ensure the shipment arrives safely while maintaining the required temperature.
The goal of monitoring cold chain shipments is to enable necessary intervention, which can help salvage products and provide data packaging engineers and third-party logistics providers (3PL) with the data to implement solutions that prevent future issues.
Cold Chain Matters
A well thought-out cold chain management strategy not only preserves product, but also protect a brand’s reputation. Shipments that fail to maintain their required temperatures can negatively impact your brand in many ways.- Business: Rejected or unsuccessful shipments can strain relationships between a brand and its distribution partners.
- Waste: Products that don’t survive the distribution environment need to be disposed of, driving up costs and impacting sustainability goals.
- Cost: Damaged shipments are costly not only for the manufacturer, but also for the carrier if they’re required to compensate the shipper for spoiled goods.
- Efficiency: Returns and product replacements increase both costs and fuel consumption.
Quick detection of temperature problems gives packaging departments the ability to minimize damage by troubleshooting shipments or rerouting the supply chain altogether. This also helps identify anomalies and enable root cause investigation, specifically when products are exchanged between CMOs and 2PL/3PL vendors.
With Adept’s help…
Developing a viable cold chain solution, requires consideration of many independent factors. The proposed solution should be systematically validated in accordance with design requirements and regulatory mandates. This process calls for extensive expertise, time and organization.Companies like Adept Group can help clients develop a standardized, repeatable process to develop cold chain solutions. We have experience leading projects from concept to commercialization. Get in touch with our team of packaging experts to discuss solutions to your cold chain challenges.