Optimizing Packaging Line Efficiency with Katie Ireland from CRB
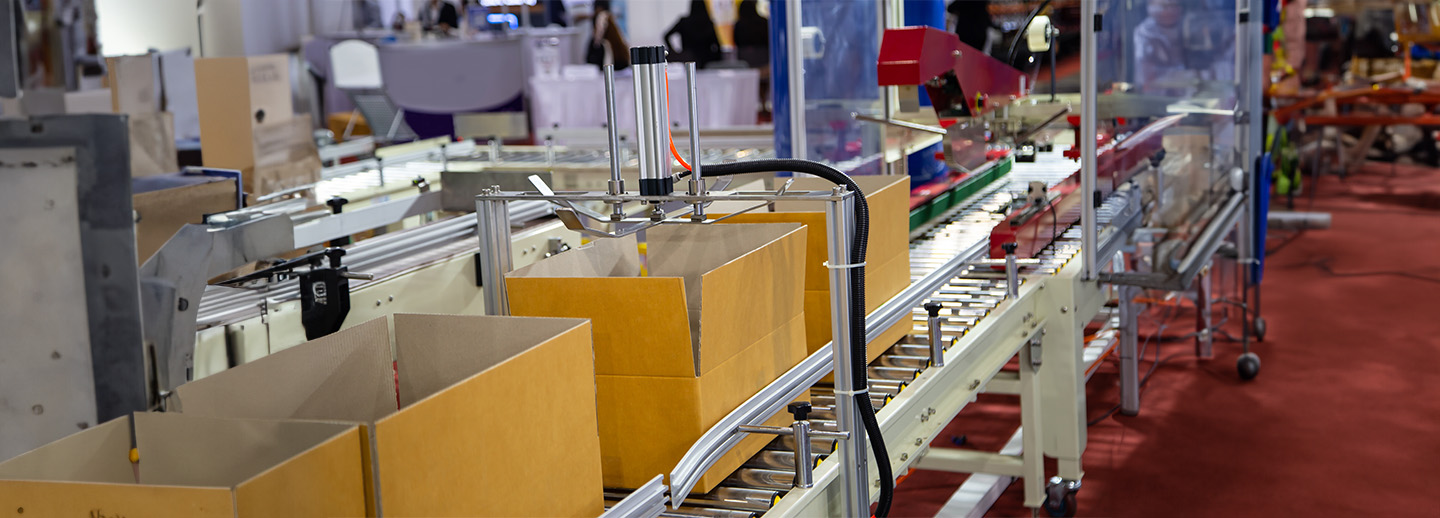
June 17,2024
Category: Cost Savings, Foundational Processes, Packaging Development
Episode Summary:
Evaluating the efficacy of your packaging line is critical to ensure every aspect of your process is streamlined and allows you to identify what intricacies you may be falling short on. Whether you’re running a single product line or optimizing for multiple, it all matters. In episode 18 of our Unpacking Excellence podcast, we speak with Andrew Dee, Principal Packaging Engineer and Strategic Growth Manager at Adept Group, and Katie Ireland, Principal Packaging Engineer at CRB, a partner of Adept Group, on key considerations for optimizing packaging line efficiency.
In this episode, we cover:
Read along below.
About Our Co-Host
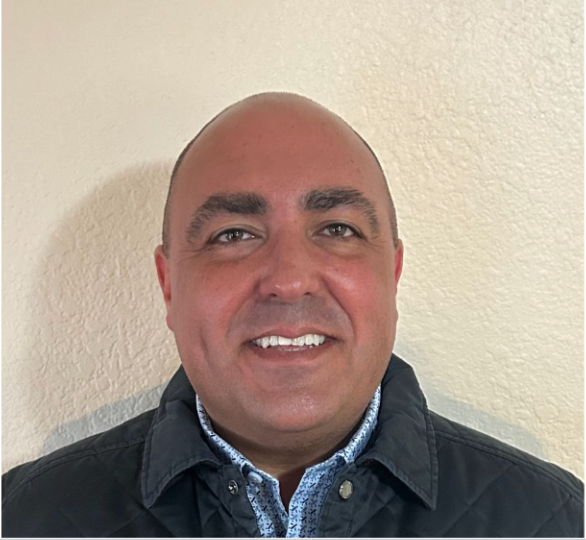-Dee.png)
Andrew (Andy) Dee, PMP
Principal Packaging Engineer and Strategic Growth Manager, Adept Group
A Michigan State University (MSU) alumnus, Andy Dee serves as Principal Packaging Engineer and Strategic Growth Manager for Adept Group and has held the role since January 2023. He helps ensure companies package, transport and store products in a safe, efficient manner while paying special attention to sustainability and costs. Andy has worked for companies in various packaging roles and received his Project Management Professional (PMP)® Certification from the Project Management Institute in August 2023.
About Our Guest
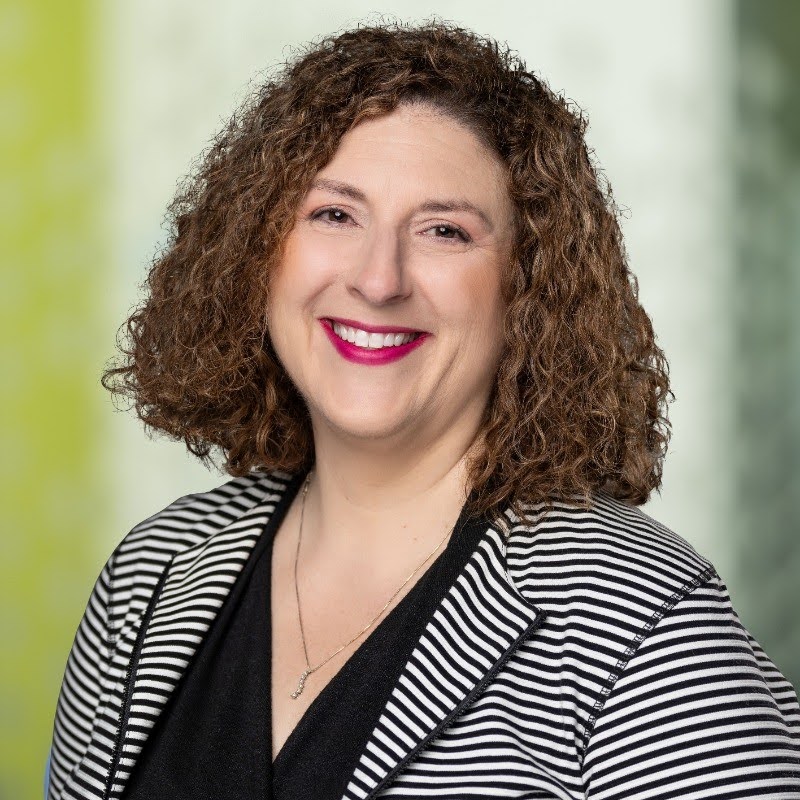
Katie Ireland
Principal Packaging Engineer, CRB
Katie Ireland is also an MSU alum who has been around the packaging industry in various roles for many well-known companies, including Ford Motor Company, Kellogg Company and Starbucks. She currently serves as a packaging engineer for CRB where she specializes in holistic packaging material and equipment design that accommodates the needs of the supply chain, operators, customers and consumers.
Listen to the Episode
0:00:01 - Intro
Powered by Adept Group, this is the Unpacking Excellence podcast, with Adept Group, bringing together top packaging professionals to share insights and knowledge on all things packaging. Now, introducing Adept Group.
0:00:22 - Adept Group
Welcome to Unpacking Excellence. Joining me today as my co-host is our Principal Engineer and Strategic Growth Manager, Andy Dee, and our guest is Katie Ireland, a Packaging Engineer with CRB. Katie and Andy, how are you doing today?
0:00:37 - Katie
I'm doing great.
0:00:38 - Andy
Good, thanks, Daniel.
0:00:40 - Adept Group
Glad to hear it. Katie, for listeners who aren't familiar with CRB, can you tell us a little more about the company and what you guys do?
0:00:48 - Katie
Absolutely, I'd be happy to. I work for CRB, and CRB stands for Clark, Richardson and Biskup. Those were the three founding members of our firm 40 years ago. This is actually our anniversary month of April, so it's 40 years to almost this week. CRB is comprised of engineering, architecture, construction and consulting services for the life science and food and beverage industries.
0:01:20 - Adept Group
Okay, and then within CRB, what is your role, and how does it relate to packaging?
0:01:25 - Katie
So my role is a packaging engineer, and I'm in the process and packaging engineering group of the food and beverage team. I'm responsible for packaging equipment selection, design, production layouts and successful production startups. Successful production startups may include packaging material design, consumer-centric design and sustainability, and, in partnership with our internal industry 4.0 experts, we can build smart manufacturing packaging lines for our clients.
0:01:58 - Adept Group
Katie, what got you into or interested in working in packaging in the first place?
0:02:05 - Katie
Oh, that's a fun story. I was introduced to the idea of packaging while working full-time in the summers at a flower shop during high school, and one of the floral designers that I knew that I was going to MSU, and she had a neighbor who had just graduated from packaging engineering at MSU, and she knew that I was going to do something in math science and that I wanted to design. So she shared with me a little bit about her neighbor and how impressed she was that she was graduating and going directly to a new location in the United States from Michigan and buying a new car and looking at houses and was just really impressed that her neighbor's daughter was set out to start her career with success. And she shared that with me. I thought going into MSU that I might want to do architectural design and interior design, which are two separate degrees, and the week before classes started, I met a friend. Her name was Kathy, and she was wearing a packaging sweatshirt.
That first week before school in the dorm cafeteria, it was breakfast time, and I saw her packaging sweatshirt and asked her if she could share a little bit about packaging, and she said she wasn't really able to do that, but her father could. Her father was Don Abbott, one of the packaging school instructors, and she told him a little bit about me, and he brought planning papers and the Packaging 101 book, along with her carpet for her dorm room. A couple of nights later, after we had talked and I took a look at the curriculum and that book, I took his introductory course and started my coursework to complete my BS in packaging. So I planned out my four years and made sure I had time for an internship. I interned at Nestle, and that was the beginning of it all.
0:04:23 - Adept Group
That is a fun story. People who don't work in packaging don't really think about it, so it's always interesting to hear how people went from not being that familiar with packaging engineering to choosing it as a career.
0:04:37 - Katie
Absolutely. It had all the elements that I was looking for. I wanted to design, and I wanted to help people. It had marketing, communication, and engineering, all of the disciplines that I was really excited about. So I was fortunate that it came to light, and I was able to follow that and pay attention. And here we are today, 30 years later, still loving it.
0:05:07 - Adept Group
Yeah, I know a lot of the folks on our team really like that and the aspect of wearing a lot of hats.
0:05:15 - Katie
Absolutely. It's never a dull moment in the packaging world. There's always something new and different, and, having been both on the owner’s and now on the engineering side, it's fascinating to see what people want to do and some of the new innovations that are out there and helping to build even awareness about what we're doing today, like around sustainability. So there's always something to learn and something new, and I love sharing that with people who want to learn more.
0:05:56 - Adept Group
The topic we really wanted to speak with you today is about optimizing packaging lines. I know you're working with some folks on our team, including Andy, on some projects in that regard. When we talk about optimizing packaging lines for existing packaging facilities, what are some of the indicators that things aren't necessarily as efficient as they could be?
0:06:19 - Katie
That's a great question. So typically when a line is not running at its optimum, the usual indicators are the throughput and having issues with what their end-of-the-line case counts are or anywhere up until that case count, quality issues with the product itself. You could also have small and large line delays on that line. It may feel unpredictable to the operator. Shutdowns of the line are often due to either equipment or material failures. Those are usually the big indicators.
0:06:59 - Andy
Yeah, one thing I always notice is, if you see a group of people at a certain segment in the line, and they're erecting boxes or something like that to try to keep things moving along, prepare for a startup, if there's a stop to make sure that they've got enough things accumulated at certain areas or if there's too much accumulation in certain areas, that's another sign that they could use some help in optimizing their lines.
0:07:29 - Adept Group
Katie, you mentioned the issues with shutdowns and things. What are some things that packaging facilities need to account for to try and minimize that downtime?
0:07:38 - Katie
Well, one of the things that they can do to minimize the downtime is to look for what the root cause might be. Why do they have to make cases in advance, or why do we have folks on the line struggling to clear something that's jammed? So really taking a critical look at what the pinpointing factors are and doing a root cause analysis is key to opening up that issue and finding the solutions to eliminate those stops.
0:08:19 - Adept Group
When we're talking about different types of packaging lines, can you talk a little bit about the differences between optimizing lines that really only run one product and lines that might run multiple products?
0:08:32 - Katie
Sure. So they're not too different. We'll just start here. It's really key, whether it's one or multiple products, to qualify each of the packaging pieces of equipment that are segments of that line with its key materials. So if you're working on a primary filler, a secondary carton and a tertiary case packer, let's say each one of those machines you want to make sure that you've got the optimal materials and settings for each size, for those designs, you could have a small bottle and a large bottle. We'll just keep it generic.
You're going to want to make sure that the small bottle is optimized with its smaller carton and smaller case for those particular settings and speeds, and then the same goes for the large bottle. You're going to want to make sure that you've got all the sizes correct, all the settings and speeds and all the integration between each piece of equipment, set up for those speeds, and then, that becomes a recipe. So you'll have a recipe for the small bottle and the large bottle. That's why I said it's not really different whether you're doing it for one product or more than one product because you're going to have to do it for each to create that optimal running recipe. Once you have that optimal speed, recipe and timing for each piece of equipment, you're going to want to understand what your limiting factor is within that line, and that's typically the product that's flowing into the packaging line.
So you're going to want to optimize the total line speed and sequencing based on that minimum and maximum flow of product. So once you've got everything dialed in on the packaging side, you want to be able to also dial in that range so that when you are sequencing from a minimum speed up to a maximum speed, it can handle it within that recipe for each size.
0:10:50 - Adept Group
When I was talking to Andy about the project you guys are working on together, he mentioned to me that it's really important to ensure that each downstream step in the packaging process is faster than the step before it to avoid bottlenecks. I realize that's probably a little bit of an oversimplification of what optimizing the process looks like, but can you at least talk about what's important about that particular aspect making sure that each step runs faster than the one before?
0:11:17 - Katie
Yeah. So it really depends on how you design your line, but typically, the rule of thumb is to have a 20% increase, and that's typical as you move from the primary packaging equipment through the secondary and then 20% from secondary into tertiary. You can also build in accumulation that can help you eliminate the impact of little microstops on the overall production line efficiency and keep the rest of the line running at a rate as the microstop is taken care of by the operator. So again, it's about a 20% increase as you move down the line, but you can also help plan out microstops with accumulation.
0:12:05 - Andy
Yeah, and I think another thing there on the microstops is also having a solid preventative maintenance schedule. And I know that sometimes, someone might not be doing what they need to be doing, and they don't really find out until after the fact when they incur all these different stops and go through the whole root cause analysis. And sometimes, it's just as simple as updating their PM schedule as well. Do you see that a lot?
0:12:31 - Katie
Yes, absolutely.
I mean, there are a lot of factors that facilities running with packaging can account for to minimize their downtime. So the scheduling of that process and packaging, making sure you've got that balanced load between the two, your operators and your support roles and making sure they're well-trained on the line, that includes being able to troubleshoot your material design and quality of supplier materials.
Consistency is key for both, and consistency also includes how you're taking care of your production lines, as you mentioned, so making sure that you're using your maintenance schedules and production lines and making sure that you're using your maintenance schedules, or, if you have predictive maintenance, paying attention to those cues when the predictive maintenance comes up. Make sure you also have inventory management for the production of those lines, and not only just to run the packaging but also to handle those pieces and parts that you need for the predictive or planned maintenance. So the key is really keeping the production lines fit for use and keeping the optimal settings for efficient production. And sometimes, that means you have to stop and really take a look at what your baseline numbers were to begin with and how far off you are from those baseline numbers to get back into your optimal running zone.
0:13:58 - Adept Group
We talked a little bit about the way that people can help keep the machine and everything running smoothly. But for processes that have some automated sections and some manual steps, are there challenges to integrating those and making sure things stay running smoothly?
0:14:16 - Katie
Yes, and it's not really too much different than when you're planning for a fully automated line. What you need to understand is what are your minimum and maximum speeds of the manual piece of that line. So that's your people, your human resources, a specific rate that includes being ergonomically safe and including breaks and expectations of the line for the shifts. Understanding how many people need to be allocated for that line for a day, and making sure that you're rotating operators that are manually a part of that line is key as well. And then, you want to basically wrap the automation around that. So how effective are the people? Then, you can create that recipe from the automation side to uptake after that portion of the operation. So it's very similar. You just need to understand your human rates and how often you've got operators rotating, paying attention to fatigue and overall throughput.
When you're talking about optimizing the equipment and the packaging line, it's not really the facility, it's the people management.
Make sure that there are processes to check the settings, keep the equipment running in their optimal windows and adhere to a maintenance schedule and indicators that the equipment and/or the people aren't working right. So it's really up to production management and operators working together to keep the lines themselves in tune and running the way they want them to. And if that isn't a daily practice built in, I highly encourage them to look at what that schedule needs to be and understand indicators. And if you can keep your running window at its optimum at all times, then you know what you need to adjust to fix issues. So if you're running outside of the optimal window, it might be because you need a part, but you need to wait for that part for a couple of weeks. So how do you optimize the settings to get what you need until you can get that part in? So it's just being smart about your choices and planning.
0:17:29 - Adept Group
Katie, I want to thank you for your time today. If people are interested in learning more about CRB Group and what you guys do, what's the best way to find more information?
0:17:38 - Katie
Certainly. They can contact me directly via email, and that's katie.ireland@crbgroup.com. You can reach me by phone, and my number is 816-955-2994. And if you're looking for some general information, you can go to www.crbgroup.com.
0:18:10 - Adept Group
Katie and Andy, thank you both for your time today.
0:18:14 - Katie
You're welcome.
0:18:15 - Andy
Thank you very much.
0:18:16 - Katie
Thank you for having us.
0:18:19 - Outro
Thank you for listening to Unpacking Excellence with Adept Group. For more resources on all things packaging, head to our website, adeptpackaging.com. Don't forget to subscribe, and thanks again for listening.
About Adept Group
Adept Group is a premier packaging partner for some of the most iconic brands in the food & beverage, CPG, pharmaceutical, medical device and industrial industries. Our team has expertise in over 60 specialized areas of focus and is the go-to for packaging needs, from cost optimization to regulatory compliance to design and engineering services. We work with clients to help them maximize the value of their packaging with personalized strategies specific to their industry and goals. Throughout the years, we’ve helped clients save hundreds of millions of dollars through cost-saving approaches to packaging that also coincide with sustainability efforts, helping build trust and credibility with consumers. If you have a packaging challenge, we’re up for it. Get in touch with our team of packaging engineering experts today to get started.
Evaluating the efficacy of your packaging line is critical to ensure every aspect of your process is streamlined and allows you to identify what intricacies you may be falling short on. Whether you’re running a single product line or optimizing for multiple, it all matters. In episode 18 of our Unpacking Excellence podcast, we speak with Andrew Dee, Principal Packaging Engineer and Strategic Growth Manager at Adept Group, and Katie Ireland, Principal Packaging Engineer at CRB, a partner of Adept Group, on key considerations for optimizing packaging line efficiency.
In this episode, we cover:
- Optimizing for single- and multi-product packaging lines
- Identifying indicators of inefficiency
- Solutions for maximizing production once indicators are analyzed
Read along below.
About Our Co-Host
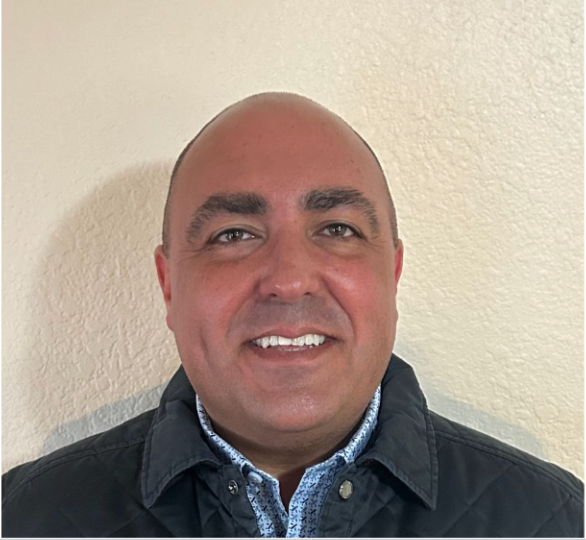-Dee.png)
Andrew (Andy) Dee, PMP
Principal Packaging Engineer and Strategic Growth Manager, Adept Group
A Michigan State University (MSU) alumnus, Andy Dee serves as Principal Packaging Engineer and Strategic Growth Manager for Adept Group and has held the role since January 2023. He helps ensure companies package, transport and store products in a safe, efficient manner while paying special attention to sustainability and costs. Andy has worked for companies in various packaging roles and received his Project Management Professional (PMP)® Certification from the Project Management Institute in August 2023.
About Our Guest
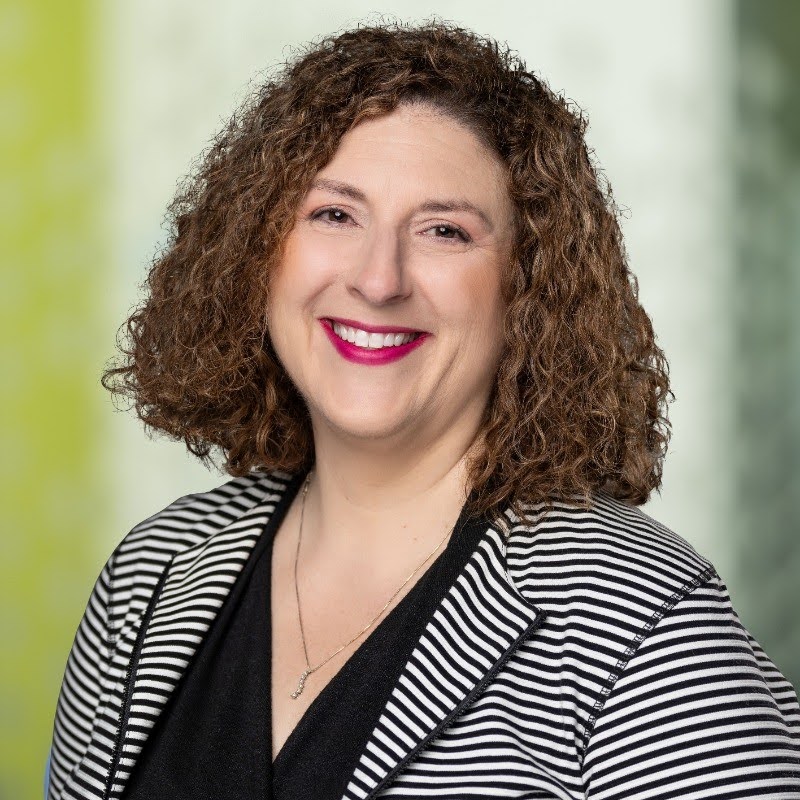
Katie Ireland
Principal Packaging Engineer, CRB
Katie Ireland is also an MSU alum who has been around the packaging industry in various roles for many well-known companies, including Ford Motor Company, Kellogg Company and Starbucks. She currently serves as a packaging engineer for CRB where she specializes in holistic packaging material and equipment design that accommodates the needs of the supply chain, operators, customers and consumers.
Listen to the Episode
0:00:01 - Intro
Powered by Adept Group, this is the Unpacking Excellence podcast, with Adept Group, bringing together top packaging professionals to share insights and knowledge on all things packaging. Now, introducing Adept Group.
0:00:22 - Adept Group
Welcome to Unpacking Excellence. Joining me today as my co-host is our Principal Engineer and Strategic Growth Manager, Andy Dee, and our guest is Katie Ireland, a Packaging Engineer with CRB. Katie and Andy, how are you doing today?
0:00:37 - Katie
I'm doing great.
0:00:38 - Andy
Good, thanks, Daniel.
0:00:40 - Adept Group
Glad to hear it. Katie, for listeners who aren't familiar with CRB, can you tell us a little more about the company and what you guys do?
0:00:48 - Katie
Absolutely, I'd be happy to. I work for CRB, and CRB stands for Clark, Richardson and Biskup. Those were the three founding members of our firm 40 years ago. This is actually our anniversary month of April, so it's 40 years to almost this week. CRB is comprised of engineering, architecture, construction and consulting services for the life science and food and beverage industries.
0:01:20 - Adept Group
Okay, and then within CRB, what is your role, and how does it relate to packaging?
0:01:25 - Katie
So my role is a packaging engineer, and I'm in the process and packaging engineering group of the food and beverage team. I'm responsible for packaging equipment selection, design, production layouts and successful production startups. Successful production startups may include packaging material design, consumer-centric design and sustainability, and, in partnership with our internal industry 4.0 experts, we can build smart manufacturing packaging lines for our clients.
0:01:58 - Adept Group
Katie, what got you into or interested in working in packaging in the first place?
0:02:05 - Katie
Oh, that's a fun story. I was introduced to the idea of packaging while working full-time in the summers at a flower shop during high school, and one of the floral designers that I knew that I was going to MSU, and she had a neighbor who had just graduated from packaging engineering at MSU, and she knew that I was going to do something in math science and that I wanted to design. So she shared with me a little bit about her neighbor and how impressed she was that she was graduating and going directly to a new location in the United States from Michigan and buying a new car and looking at houses and was just really impressed that her neighbor's daughter was set out to start her career with success. And she shared that with me. I thought going into MSU that I might want to do architectural design and interior design, which are two separate degrees, and the week before classes started, I met a friend. Her name was Kathy, and she was wearing a packaging sweatshirt.
That first week before school in the dorm cafeteria, it was breakfast time, and I saw her packaging sweatshirt and asked her if she could share a little bit about packaging, and she said she wasn't really able to do that, but her father could. Her father was Don Abbott, one of the packaging school instructors, and she told him a little bit about me, and he brought planning papers and the Packaging 101 book, along with her carpet for her dorm room. A couple of nights later, after we had talked and I took a look at the curriculum and that book, I took his introductory course and started my coursework to complete my BS in packaging. So I planned out my four years and made sure I had time for an internship. I interned at Nestle, and that was the beginning of it all.
0:04:23 - Adept Group
That is a fun story. People who don't work in packaging don't really think about it, so it's always interesting to hear how people went from not being that familiar with packaging engineering to choosing it as a career.
0:04:37 - Katie
Absolutely. It had all the elements that I was looking for. I wanted to design, and I wanted to help people. It had marketing, communication, and engineering, all of the disciplines that I was really excited about. So I was fortunate that it came to light, and I was able to follow that and pay attention. And here we are today, 30 years later, still loving it.
0:05:07 - Adept Group
Yeah, I know a lot of the folks on our team really like that and the aspect of wearing a lot of hats.
0:05:15 - Katie
Absolutely. It's never a dull moment in the packaging world. There's always something new and different, and, having been both on the owner’s and now on the engineering side, it's fascinating to see what people want to do and some of the new innovations that are out there and helping to build even awareness about what we're doing today, like around sustainability. So there's always something to learn and something new, and I love sharing that with people who want to learn more.
0:05:56 - Adept Group
The topic we really wanted to speak with you today is about optimizing packaging lines. I know you're working with some folks on our team, including Andy, on some projects in that regard. When we talk about optimizing packaging lines for existing packaging facilities, what are some of the indicators that things aren't necessarily as efficient as they could be?
0:06:19 - Katie
That's a great question. So typically when a line is not running at its optimum, the usual indicators are the throughput and having issues with what their end-of-the-line case counts are or anywhere up until that case count, quality issues with the product itself. You could also have small and large line delays on that line. It may feel unpredictable to the operator. Shutdowns of the line are often due to either equipment or material failures. Those are usually the big indicators.
0:06:59 - Andy
Yeah, one thing I always notice is, if you see a group of people at a certain segment in the line, and they're erecting boxes or something like that to try to keep things moving along, prepare for a startup, if there's a stop to make sure that they've got enough things accumulated at certain areas or if there's too much accumulation in certain areas, that's another sign that they could use some help in optimizing their lines.
0:07:29 - Adept Group
Katie, you mentioned the issues with shutdowns and things. What are some things that packaging facilities need to account for to try and minimize that downtime?
0:07:38 - Katie
Well, one of the things that they can do to minimize the downtime is to look for what the root cause might be. Why do they have to make cases in advance, or why do we have folks on the line struggling to clear something that's jammed? So really taking a critical look at what the pinpointing factors are and doing a root cause analysis is key to opening up that issue and finding the solutions to eliminate those stops.
0:08:19 - Adept Group
When we're talking about different types of packaging lines, can you talk a little bit about the differences between optimizing lines that really only run one product and lines that might run multiple products?
0:08:32 - Katie
Sure. So they're not too different. We'll just start here. It's really key, whether it's one or multiple products, to qualify each of the packaging pieces of equipment that are segments of that line with its key materials. So if you're working on a primary filler, a secondary carton and a tertiary case packer, let's say each one of those machines you want to make sure that you've got the optimal materials and settings for each size, for those designs, you could have a small bottle and a large bottle. We'll just keep it generic.
You're going to want to make sure that the small bottle is optimized with its smaller carton and smaller case for those particular settings and speeds, and then the same goes for the large bottle. You're going to want to make sure that you've got all the sizes correct, all the settings and speeds and all the integration between each piece of equipment, set up for those speeds, and then, that becomes a recipe. So you'll have a recipe for the small bottle and the large bottle. That's why I said it's not really different whether you're doing it for one product or more than one product because you're going to have to do it for each to create that optimal running recipe. Once you have that optimal speed, recipe and timing for each piece of equipment, you're going to want to understand what your limiting factor is within that line, and that's typically the product that's flowing into the packaging line.
So you're going to want to optimize the total line speed and sequencing based on that minimum and maximum flow of product. So once you've got everything dialed in on the packaging side, you want to be able to also dial in that range so that when you are sequencing from a minimum speed up to a maximum speed, it can handle it within that recipe for each size.
0:10:50 - Adept Group
When I was talking to Andy about the project you guys are working on together, he mentioned to me that it's really important to ensure that each downstream step in the packaging process is faster than the step before it to avoid bottlenecks. I realize that's probably a little bit of an oversimplification of what optimizing the process looks like, but can you at least talk about what's important about that particular aspect making sure that each step runs faster than the one before?
0:11:17 - Katie
Yeah. So it really depends on how you design your line, but typically, the rule of thumb is to have a 20% increase, and that's typical as you move from the primary packaging equipment through the secondary and then 20% from secondary into tertiary. You can also build in accumulation that can help you eliminate the impact of little microstops on the overall production line efficiency and keep the rest of the line running at a rate as the microstop is taken care of by the operator. So again, it's about a 20% increase as you move down the line, but you can also help plan out microstops with accumulation.
0:12:05 - Andy
Yeah, and I think another thing there on the microstops is also having a solid preventative maintenance schedule. And I know that sometimes, someone might not be doing what they need to be doing, and they don't really find out until after the fact when they incur all these different stops and go through the whole root cause analysis. And sometimes, it's just as simple as updating their PM schedule as well. Do you see that a lot?
0:12:31 - Katie
Yes, absolutely.
I mean, there are a lot of factors that facilities running with packaging can account for to minimize their downtime. So the scheduling of that process and packaging, making sure you've got that balanced load between the two, your operators and your support roles and making sure they're well-trained on the line, that includes being able to troubleshoot your material design and quality of supplier materials.
Consistency is key for both, and consistency also includes how you're taking care of your production lines, as you mentioned, so making sure that you're using your maintenance schedules and production lines and making sure that you're using your maintenance schedules, or, if you have predictive maintenance, paying attention to those cues when the predictive maintenance comes up. Make sure you also have inventory management for the production of those lines, and not only just to run the packaging but also to handle those pieces and parts that you need for the predictive or planned maintenance. So the key is really keeping the production lines fit for use and keeping the optimal settings for efficient production. And sometimes, that means you have to stop and really take a look at what your baseline numbers were to begin with and how far off you are from those baseline numbers to get back into your optimal running zone.
0:13:58 - Adept Group
We talked a little bit about the way that people can help keep the machine and everything running smoothly. But for processes that have some automated sections and some manual steps, are there challenges to integrating those and making sure things stay running smoothly?
0:14:16 - Katie
Yes, and it's not really too much different than when you're planning for a fully automated line. What you need to understand is what are your minimum and maximum speeds of the manual piece of that line. So that's your people, your human resources, a specific rate that includes being ergonomically safe and including breaks and expectations of the line for the shifts. Understanding how many people need to be allocated for that line for a day, and making sure that you're rotating operators that are manually a part of that line is key as well. And then, you want to basically wrap the automation around that. So how effective are the people? Then, you can create that recipe from the automation side to uptake after that portion of the operation. So it's very similar. You just need to understand your human rates and how often you've got operators rotating, paying attention to fatigue and overall throughput.
When you're talking about optimizing the equipment and the packaging line, it's not really the facility, it's the people management.
Make sure that there are processes to check the settings, keep the equipment running in their optimal windows and adhere to a maintenance schedule and indicators that the equipment and/or the people aren't working right. So it's really up to production management and operators working together to keep the lines themselves in tune and running the way they want them to. And if that isn't a daily practice built in, I highly encourage them to look at what that schedule needs to be and understand indicators. And if you can keep your running window at its optimum at all times, then you know what you need to adjust to fix issues. So if you're running outside of the optimal window, it might be because you need a part, but you need to wait for that part for a couple of weeks. So how do you optimize the settings to get what you need until you can get that part in? So it's just being smart about your choices and planning.
0:17:29 - Adept Group
Katie, I want to thank you for your time today. If people are interested in learning more about CRB Group and what you guys do, what's the best way to find more information?
0:17:38 - Katie
Certainly. They can contact me directly via email, and that's katie.ireland@crbgroup.com. You can reach me by phone, and my number is 816-955-2994. And if you're looking for some general information, you can go to www.crbgroup.com.
0:18:10 - Adept Group
Katie and Andy, thank you both for your time today.
0:18:14 - Katie
You're welcome.
0:18:15 - Andy
Thank you very much.
0:18:16 - Katie
Thank you for having us.
0:18:19 - Outro
Thank you for listening to Unpacking Excellence with Adept Group. For more resources on all things packaging, head to our website, adeptpackaging.com. Don't forget to subscribe, and thanks again for listening.
About Adept Group
Adept Group is a premier packaging partner for some of the most iconic brands in the food & beverage, CPG, pharmaceutical, medical device and industrial industries. Our team has expertise in over 60 specialized areas of focus and is the go-to for packaging needs, from cost optimization to regulatory compliance to design and engineering services. We work with clients to help them maximize the value of their packaging with personalized strategies specific to their industry and goals. Throughout the years, we’ve helped clients save hundreds of millions of dollars through cost-saving approaches to packaging that also coincide with sustainability efforts, helping build trust and credibility with consumers. If you have a packaging challenge, we’re up for it. Get in touch with our team of packaging engineering experts today to get started.