Single Parcel Distribution Test Design for E-Commerce
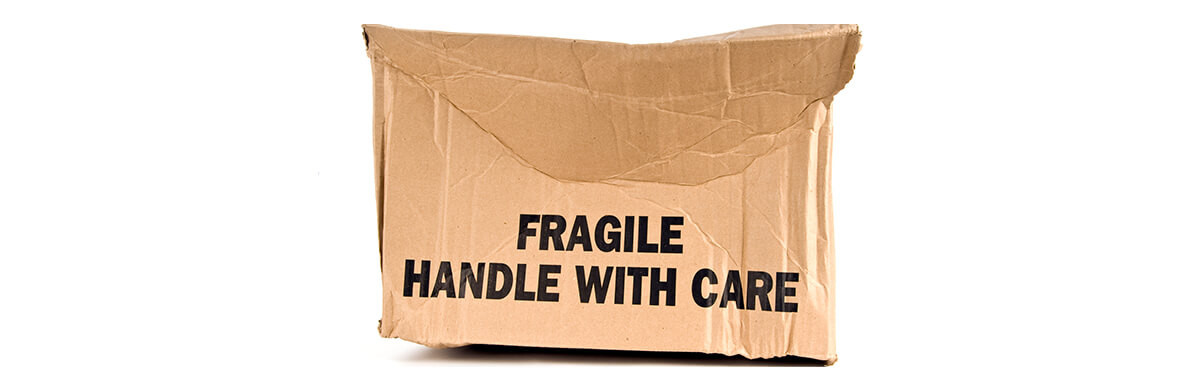
The COVID-19 pandemic has provided a major boost to e-commerce, with the U.S. Census Bureau reporting a 45% year-over-year increase from the second quarter of 2019 to the second quarter of 2020. For brands experiencing a significant increase in e-commerce sales or embracing e-commerce for the first time, designing packaging to hold up under the conditions a single parcel may face in shipping can be a challenge. Products that are damaged during shipping are costly to your brand’s reputation and can ruin your relationship with customers.
Testing your packaging to ensure it can protect the product at all points along its journey from your packaging line to its final destination is integral to the process and to your brand. While the process can be daunting, there are two main things you need to understand before you get started: the distribution environment your product and its packaging will encounter during shipping and the available testing standards that simulate how your package will perform in that environment.
Know Your Distribution Environment
Distribution environments can be complicated. Depending on the product, a package may encounter a wide variety of conditions between packaging and arrival at its final destination. These conditions can be broken down into two main categories, ambient conditions and handling conditions.
Ambient Conditions
Ambient conditions can vary wildly depending on the distance your package will travel and the geographic location(s) it will travel through. Factors to consider include the humidity it will experience, the range in temperatures it will face and how much exposure it will have to elements such as sun light and, potentially, precipitation. Some products may even need to remain refrigerated or frozen during shipping to preserve quality.
Handling Conditions
Handling conditions have a similarly broad range and depend on whether your packaging will ship via rail, truck, air or some combination of the three. While we’re primarily focusing on products that will ship as single parcels, there may be portions of their journey where they travel as part of a unitized load. Packaging decisions can also vary depending on whether a package is primarily hand-carried or if it will be lifted with a crane or forklift. At times, other packages may be stacked on top of it, meaning the package will need to support additional weight without being crushed.
Insights from Technology
While an expert can make a fairly accurate projection about the conditions a package will face in the distribution environment, there are ways to take some of the guesswork out of the process. Several companies make small, disposable sensors that can be placed in test packages and shipped through the normal distribution channels to capture a variety of information about shock, temperature and sunlight, along with location and time, to provide an opportunity for real-time data analysis.
Know Your Testing Standards
There are two main bodies that issue widely accepted single parcel test standards. ASTM is one of the world’s largest international organizations that develops standards. It is comprised of a large group of experts who develop and democratically approve those standards. The other organization, ISTA is a private industry association with standards generated by its board of directors. While the standards developed by both organizations are valuable, ASTM standards are more widely accepted than ISTA standards. For food and beverage brands, for example, the FDA recognizes more than 400 ASTM standards, but recognizes only the ISTA 3A, 3B and 3E series.
These organizations have developed hundreds of standards that cover the wide variety of options for packaging sizes, shapes and materials. It would be impossible to summarize all of them here, but an example that compares a few of the available standards is helpful in illustrating the relationship between knowing your distribution environment and knowing what options are available for testing. The table below lays out the steps in three testing standards that can be applied to double-walled carton that is 1.8 cubic feet in size and weighs 5 lbs.
Testing Standards Example
Step | ISTA 3A Series | ASTM D4169 DC 13 AL II | ASTM D7386 |
1 | Precondition to ambient for 12 hours | Condition to adjusted settings from standard of 73.4 +/- 2°F (23 +/- 1°C) and 50% +/- 2% for 72 hours | Condition to adjusted settings from standard of 73.4 +/- 2°F (23 +/- 1°C) and 50% +/- 2% for 24 hours |
2 | Condition to determined temperature and humidity “Controlled” conditions will use 73°F and 50% humidity for 72 hours | Handling – Six drops from 15” | Handling – Four drops from 18” and two drops from 20” |
3 | Shock – Eight drops from 18” plus one drop from 36” | Vehicle Stacking – Apply and release 278lbs | Vibration under Compressive Load – Bottom face for 60 minutes and side face for 30 minutes |
4 | Vibration – Random with overall Grms level of .46Grms and with 105lbs topload for total of 120 minutes | Loose Load Vibration - Fixed Displacement for 30 minutes | High Altitude (optional) |
5 | Vibration – Random with overall Grms level of .46Grms for total of 30 minutes | Low pressure (optional) | Handling – Two drops from 20” and four drops from 18” |
6 | Shock – Seven drops from 18” plus one drop from 36” | Vehicle Vibration - Random60min with overall Grms level of 0.54120 min with overall Grms level of 1.05 | Vibration – Bottom face for 30 minutes and side face for 30 minutes |
7 | n/a | Handling – Five drops from 15” plus one drop from 30” | Handling – Two drops from 14”, three from 20” and one from 32” |
8 | n/a | n/a | Concentrated Impact – Drop height 36” |
The details included for each step are instructive in deciding which standard best applies to your package and its distribution environment. Differences include the temperatures the packages are exposed to during testing, drop heights, the amount of compression force applied to the package, and other factors. ISTA 3A requires dropping the package from a height of 18 inches
seven times and a height of 36 inches once, while ASTM D4169 DC 13 AL II calls for five drops from 15 inches and one from 30 inches. A thorough understand of your package’s shipping environment will help you decide which of those standards best simulates the conditions your package is likely to encounter.
Get Help from the Experts
The wide variety of conditions a package may encounter in its distribution environment and the long list of available testing standards from ASTM and ISTA can make designing distribution tests for single parcels a daunting task, but a knowledgeable packaging engineer with experience designing and testing packages for e-commerce distribution can help you guide you through the process.
For more information in single parcel testing, you can watch our recent Learning Share webinar on the topic or download our white paper, which focuses on single parcel testing for medical devices.
If you need help developing new packaging or updating your existing packaging to better withstand the e-commerce distribution environment, get in touch. Our team has led this process for some of the most iconic brands in the food, beverage, CPG and life sciences industries.